10 Best Practices for Effective Inventory Management
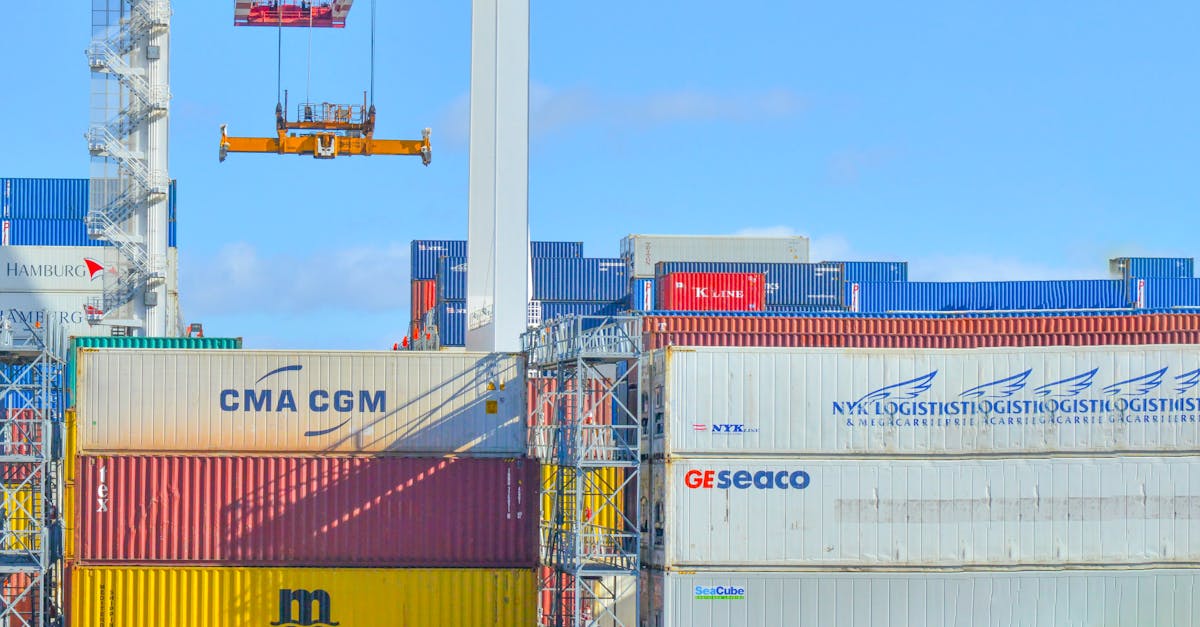
Categorise Your Inventory
Effective inventory management begins with a clear understanding of what you have in stock. Grouping products into categories based on criteria such as demand, value, or type can lead to better control and visibility. This method not only simplifies tracking but also assists in identifying slow-moving items. By categorising inventory, businesses can allocate resources more efficiently, ensuring that space is optimised and that necessary stock levels are maintained.
Utilising systems like the ABC Analysis Method adds further structure to inventory categorisation. This approach segments products into three categories: A items, which are high-value but low-quantity; B items, which are moderate in both value and quantity; and C items, characterised by low-value yet high-quantity. Prioritising management efforts based on this categorisation ensures that resources are directed towards the most critical stock, ultimately enhancing overall efficiency and responsiveness to market demands.
Using the ABC Analysis Method
ABC analysis is an inventory categorisation technique that helps businesses focus on the most important items in their inventory. Items are divided into three categories: A, B, and C. The A items are of high importance, representing a small percentage of the total inventory but accounting for a large portion of the overall value. B items are of moderate importance, while C items are of low importance and typically make up the largest percentage of items in stock. This method allows companies to allocate their resources and management efforts more effectively.
By prioritising inventory management based on this classification, businesses can streamline operations and reduce costs. For A items, more frequent monitoring and tighter control are necessary. B items require regular oversight, while C items may only need periodic reviews. This strategic approach enables companies to optimise their inventory holdings, minimise stockouts, and improve cash flow by ensuring that the focus remains on the items that contribute the most to the bottom line.
Optimise Warehouse Layout
An efficient warehouse layout significantly impacts inventory management and overall operational effectiveness. Organising storage areas can enhance the flow of goods, improve picking accuracy, and reduce retrieval time. A well-planned space can facilitate faster stock movement, ensuring that popular items are easily accessible while less frequently purchased goods remain stocked but out of the way. Implementing a logical zoning system for different product categories helps streamline processes, enabling staff to locate and manage products with minimal disruption.
The physical arrangement of the warehouse should also consider equipment placement and staff workflow. Strategically positioned shelves and workstations improve accessibility and reduce unnecessary movement, which saves time and energy. Utilising vertical space can maximise storage capacity, while dedicated areas for incoming and outgoing shipments prevent congestion. Regular evaluations and adjustments to the layout can ensure that it adapts to changing inventory levels or product lines, optimising operations over time.
Enhancing Efficiency through Strategic Organisation
Strategic organisation within a warehouse can significantly improve efficiency. By implementing a layout that minimises unnecessary movement, employees can access items quickly. Grouping similar products together can reduce the time spent searching for stock. Establishing clear pathways and designated zones for different types of inventory helps streamline the picking process. Using vertical space effectively also allows for maximised storage capacity, ensuring that high-turnover items are easily reachable.
Incorporating technology into the organisation can further enhance operational flow. Inventory management systems aid in tracking stock levels and locations. Barcode scanning systems can speed up the picking and packing processes by providing real-time data. Training staff to utilise these technologies ensures that they are not only familiar with the tools available but also understand how to optimise their workflow. A well-organised warehouse environment directly contributes to reduced errors and improved productivity, ultimately benefiting the entire inventory management system.
Train Your Staff Effectively
Providing comprehensive training for employees is crucial in maximising the efficiency of inventory management. Staff members equipped with knowledge about inventory systems, stock handling, and safety protocols can significantly reduce errors and improve overall productivity. It is important to integrate both theoretical and practical components into the training curriculum, ensuring that employees understand not only the processes but also the rationale behind them. Regular workshops and refresher courses can help maintain high levels of competency.
Additionally, fostering a culture of continuous learning within the organisation can lead to better outcomes. Encouraging employees to stay updated on industry trends and advancements in technology allows for the adoption of innovative practices. By empowering staff with current knowledge, they become more adaptable to changes and can proactively contribute to enhancing the inventory management process. Effective training programmes ultimately lead to heightened employee confidence and improved performance throughout the inventory lifecycle.
Importance of Staff Knowledge and Skills
Well-trained staff play a critical role in the success of inventory management. Their knowledge of the inventory system allows for accurate tracking and reporting of stock levels. Staff who understand the nuances of inventory procedures can quickly address discrepancies and minimise errors. A solid grasp of inventory management concepts ensures that employees can effectively manage stock rotations and optimise replenishment processes.
Moreover, enhancing staff skills through regular training sessions promotes confidence and efficiency. Familiarity with the latest software and technologies can significantly improve workflows. Employees equipped with comprehensive knowledge can better handle unexpected challenges. This proactive approach fosters a more responsive team capable of supporting the overall goals of the organisation. Investing in staff development leads to lower turnover and higher job satisfaction, ultimately benefiting inventory performance.
FAQS
What is the ABC analysis method in inventory management?
The ABC analysis method is a categorisation technique that divides inventory into three categories (A, B, and C) based on their importance and value. 'A' items are the most valuable, 'B' items are moderately valuable, and 'C' items are the least valuable. This helps businesses prioritise their management efforts.
How can I optimise my warehouse layout for better inventory management?
Optimising your warehouse layout involves strategically organising your storage areas to enhance efficiency. This includes placing high-demand items closer to the shipping area, using clear signage for navigation, and ensuring there is adequate space for movement to avoid bottlenecks.
Why is staff training important for effective inventory management?
Staff training is crucial because knowledgeable employees are better equipped to manage inventory efficiently. They understand the processes, can identify issues promptly, and contribute to reducing errors, which ultimately enhances overall operational productivity.
What are some common mistakes to avoid in inventory management?
Common mistakes include failing to regularly review inventory levels, neglecting to categorise products effectively, overstocking or understocking items, and not training staff adequately. Avoiding these pitfalls can lead to improved efficiency and cost savings.
How often should I review my inventory management practices?
It is advisable to review your inventory management practices regularly, at least quarterly or biannually. This frequency allows you to adapt to changing market conditions, assess the effectiveness of your current strategies, and make necessary adjustments to enhance efficiency.
Related Links
Roundup of Key Trends in Supply Chain StrategyHistorical Evolution of Supply Chain Management
Review of Top Demand Forecasting Tools
Why Supply Chain Strategy Matters in Today's Market
Why Logistics Performance Measurement is Crucial for Success
What to Consider When Building Supplier Relationships