7 essential metrics for logistics performance measurement
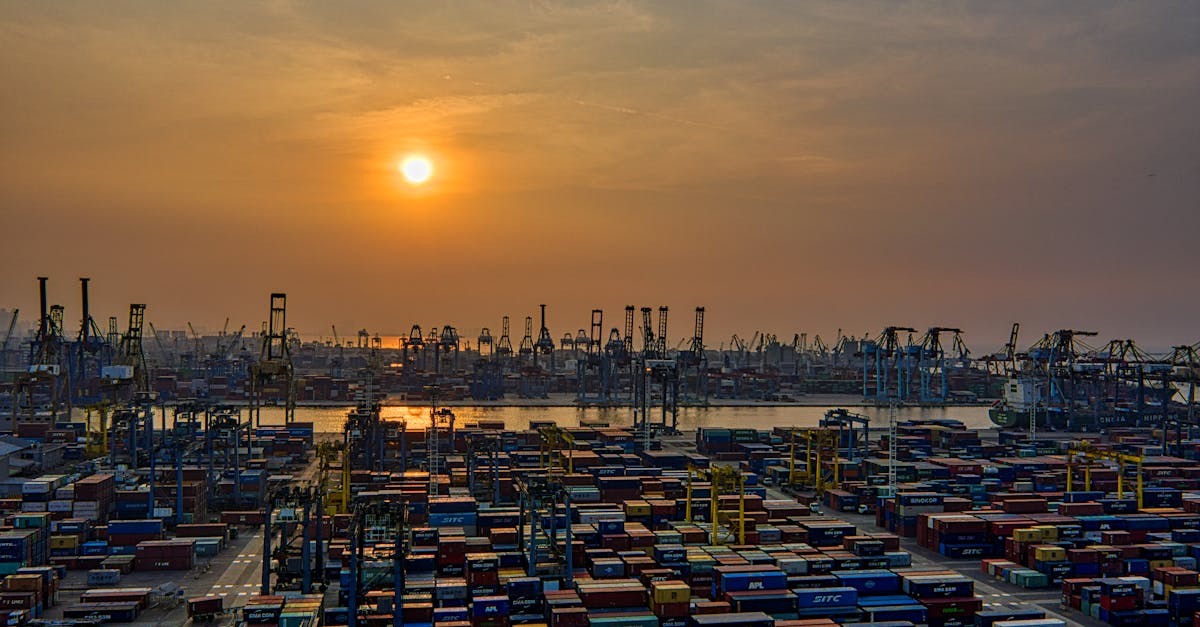
Warehouse Utilisation
Warehouse utilisation is a critical component of logistics performance measurement. It refers to the percentage of available storage space that is being effectively utilised. High utilisation rates indicate that the warehouse is operating efficiently, maximising the use of both vertical and horizontal space. In contrast, low rates can signify wasted resources and potential inefficiencies. Understanding these metrics can aid in identifying areas for improvement and optimising operations.
Maximising space and efficiency in storage relies on careful planning and organisation. Implementing systematic inventory management techniques can contribute to better utilisation rates. Approaches such as categorising products by volume or turnover can help ensure that frequently accessed items are readily available, reducing search times. Additionally, regular audits of storage space and inventory levels can highlight underused areas and facilitate smarter resource allocation, ultimately leading to more effective warehouse operations.
Maximising Space and Efficiency in Storage
Effective warehouse management relies heavily on maximising storage space while maintaining operational efficiency. Implementing well-organised shelving systems can significantly enhance space utilisation. Vertical storage options are particularly beneficial, allowing for the use of height in warehouses. Regular assessments of inventory levels help determine optimal storage needs and prevent overcrowding. Moreover, consolidating items with similar characteristics not only saves space but also simplifies the picking process.
Investing in technology solutions such as warehouse management systems (WMS) can further improve efficiency. These systems provide real-time data on inventory levels, enabling better decision-making regarding space allocation. Automated storage and retrieval systems (AS/RS) reduce the time spent locating products. Training staff on best practices also plays a vital role, as knowledgeable employees can optimise workflows and maintain an orderly environment. Enhanced organisation leads to quicker access to items, ultimately contributing to overall operational success.
Fill Rate
Fill rate is a critical metric that reflects the effectiveness of a company's inventory management and order fulfilment processes. It measures the percentage of customer orders that are fulfilled in full and on time. A higher fill rate indicates better inventory control and customer satisfaction, while a lower rate may suggest issues such as stockouts or inefficiencies in the supply chain. Companies strive to maintain a high fill rate to enhance customer loyalty and ensure that they remain competitive in the market.
To accurately assess fill rate, businesses should track it consistently across different product lines and customer segments. Analysis helps identify patterns and potential areas for improvement. Factors influencing fill rate include lead times, order processing efficiency, and stock levels. Addressing these areas can lead to increased fill rates, ultimately driving sales and fostering positive customer experiences.
Measuring the Effectiveness of Order Fulfilment
A critical aspect of evaluating logistics performance revolves around understanding the fill rate, which reflects the efficiency of order fulfilment. This metric measures the percentage of customer orders that are delivered in full and on time. A high fill rate indicates effective inventory management and a streamlined order processing system, leading to improved customer satisfaction. Conversely, a lower fill rate can signal issues such as stock shortages, ineffective picking processes, or delays in shipment.
To enhance order fulfilment effectiveness, organisations often implement strategies focused on optimising their supply chain operations. Employing robust inventory management systems enables real-time tracking of stock levels, ensuring that products are readily available to meet demand. Additionally, regular analysis of order fulfilment metrics helps identify bottlenecks in the process, allowing logistics teams to develop targeted solutions that improve overall efficiency and performance.
Cycle Time
Cycle time refers to the total time taken from the initiation of a process to its completion within the supply chain. This metric encompasses various phases, including order picking, packing and transportation, providing a comprehensive view of the efficiency of logistics operations. By understanding cycle time, businesses can identify bottlenecks and streamline workflows. Optimising this measure often leads to improved customer satisfaction as orders are fulfilled more quickly.
Monitoring cycle time continually enables organisations to assess performance and implement strategies for enhancement. Collaboration across departments, such as sales and procurement, can lead to better forecasting and inventory management. Additionally, advanced technology and automation can significantly reduce cycle times by minimising manual tasks and enhancing operational speed. This focus on cycle time not only supports cost reduction but also increases competitive advantage in a rapidly evolving market.
Understanding the Duration of Processes in the Supply Chain
Cycle time plays a pivotal role in assessing the efficiency of supply chain operations. It encapsulates the total time taken for a product to move through the various stages of the supply chain, from initial order to final delivery. Tracking this metric allows organisations to pinpoint delays and bottlenecks, facilitating timely interventions that can streamline processes and enhance overall productivity.
In-depth analysis of cycle time provides valuable insights into individual process durations, enabling businesses to identify which segments of their operations may require optimisation. Discrepancies in timeframes can reveal underlying issues related to inventory management, order processing, or transportation logistics. By addressing these areas, companies can achieve a more responsive supply chain, ultimately improving customer satisfaction and reducing operational costs.
FAQS
What are the essential metrics for logistics performance measurement?
The essential metrics include warehouse utilisation, fill rate, and cycle time, among others, which help assess the efficiency and effectiveness of logistics operations.
Why is warehouse utilisation important in logistics?
Warehouse utilisation is important because it measures how effectively storage space is being used, which can lead to improved efficiency and reduced operational costs.
What is the fill rate, and why is it significant?
The fill rate indicates the percentage of customer orders that are fulfilled completely and on time, making it a critical metric for assessing the effectiveness of order fulfilment.
How does cycle time impact supply chain performance?
Cycle time measures the duration of processes in the supply chain, and shorter cycle times typically correlate with faster delivery and increased customer satisfaction.
Can these metrics be used in conjunction with one another?
Yes, these metrics can be used in conjunction to provide a comprehensive overview of logistics performance, helping to identify areas for improvement and optimisation.
Related Links
Review of top logistics performance measurement toolsWhy logistics performance measurement is crucial for success
Roundup of best practices for logistics performance evaluation
Historical evolution of logistics performance measurement
What to include in a logistics performance measurement framework