How to Implement Best Practices in Distribution Centre Operations
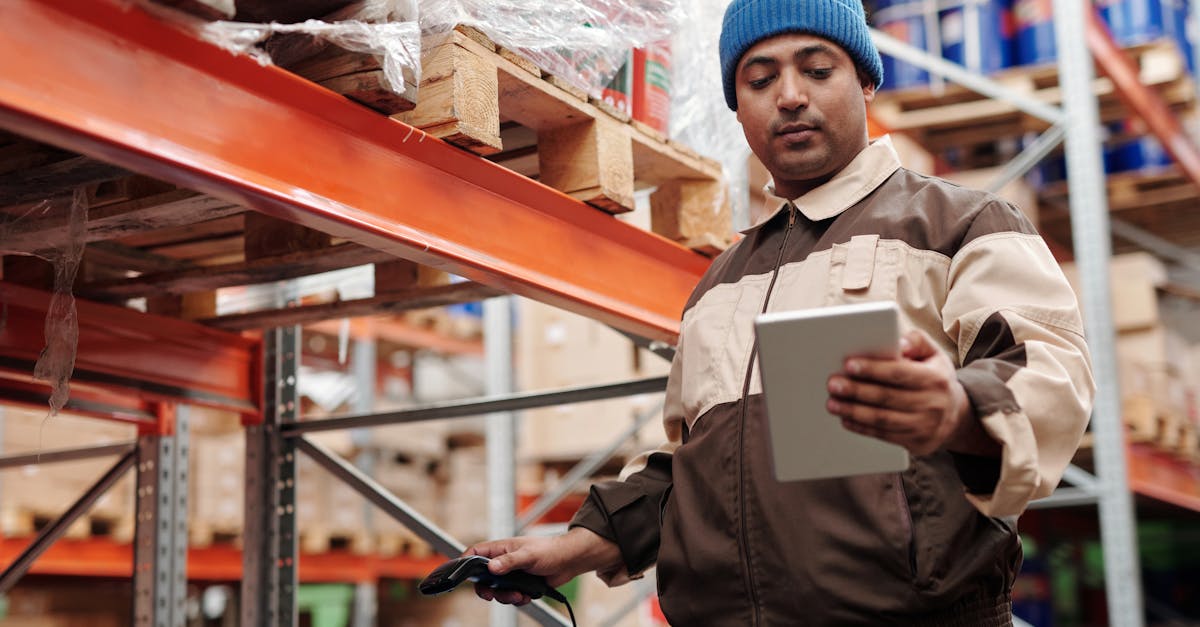
Safety Protocols in the Workplace
Employee safety remains a top priority in distribution centres. Implementing comprehensive safety protocols can significantly reduce workplace accidents. Regular training sessions help enhance employee awareness of potential hazards. Personal protective equipment (PPE) should be mandatory, with regular inspections to ensure items are in good condition. Clearly marked emergency exits and accessible first-aid kits are essential elements that contribute to a safer working environment.
Establishing a culture of safety involves encouraging employees to report unsafe conditions without fear of reprisal. Routine safety audits can identify risks and areas for improvement. Involving team members in safety discussions fosters a sense of ownership and responsibility for workplace safety. By prioritising these protocols, distribution centres can create an environment conducive to both employee well-being and operational efficiency.
Implementing Best Practices for Employee Safety
Ensuring a safe working environment in distribution centres requires a proactive approach to employee safety. Regular training sessions can equip staff with essential skills to recognise hazards and respond to emergencies. It is crucial to establish clear communication channels for reporting safety concerns. Encouraging employees to participate in safety audits fosters a culture of accountability and vigilance. Incorporating safety gear into daily operations further enhances protection against workplace accidents.
Additionally, implementing ergonomic practices can reduce the risk of injury. Providing adjustable equipment can help accommodate different body types and promote comfortable work postures. Frequent breaks should be encouraged to alleviate strain during repetitive tasks. Monitoring workloads and ensuring staff do not exceed safe limits also contribute to a healthier workplace. By consistently applying these practices, distribution centres can significantly improve overall employee well-being and safety standards.
Sustainable Practices in Distribution
Sustainability is becoming increasingly important in distribution. Implementing eco-friendly practices not only helps protect the environment but also enhances the company's reputation. Many distribution centres are exploring renewable energy sources. Solar panels and wind turbines can significantly reduce reliance on non-renewable power. Additionally, integrating energy-efficient machinery and lighting systems can decrease overall energy consumption.
Waste management plays a crucial role in sustainable distribution operations. Centres can adopt recycling programs to minimise waste sent to landfills. Composting organic waste contributes to a circular economy. Moreover, optimising packaging materials can lead to reduced plastic usage. Emphasising sustainable transportation methods helps mitigate carbon emissions. Investing in electric or hybrid vehicles reduces the overall environmental impact of logistics.
Reducing Environmental Impact
Embracing sustainability within distribution centres involves evaluating and minimising energy consumption. Upgrading to energy-efficient lighting and utilising natural daylight can significantly reduce electricity use. Implementing smart technology to monitor and control energy consumption enhances efficiency. Additionally, optimising heating and cooling systems is essential to creating a comfortable working environment while conserving energy.
The choice of materials and packaging also plays a crucial role in reducing waste. Switching to biodegradable packaging materials limits landfill contributions and promotes recycling efforts. Encouraging suppliers to adopt eco-friendly practices can further enhance sustainability throughout the supply chain. Furthermore, regularly auditing waste management processes helps identify areas for improvement and ensures compliance with environmental regulations.
Performance Metrics and KPIs
Establishing performance metrics and key performance indicators (KPIs) is essential for optimising distribution centre operations. These metrics provide measurable goals that help management assess efficiency, productivity, and the overall effectiveness of processes. Common KPIs include order accuracy, average delivery time, and inventory turnover rates. Tracking these indicators enables organisations to identify areas that require improvement and adjust strategies accordingly to enhance operational performance.
Data collected through these metrics also aids in benchmarking against industry standards and competitors. Regularly analysing performance results fosters a culture of continuous improvement within the workforce. Employees can be empowered to contribute suggestions for optimising workflows based on insight drawn from these performance indicators. Engaging staff in this process not only drives accountability but also enhances job satisfaction and overall productivity within the distribution centre.
Measuring Success in Distribution Operations
Measuring success in distribution operations requires a careful selection of performance metrics and key performance indicators (KPIs). Essential metrics include order accuracy, inventory turnover, and on-time delivery rates. These figures provide a comprehensive view of operational efficiency and help identify areas requiring improvement. Regular tracking of these metrics allows businesses to benchmark their performance against industry standards, promoting a culture of continuous improvement.
In addition to quantitative metrics, qualitative assessments play a role in evaluating operational success. Customer satisfaction surveys and employee feedback can reveal insights into service quality and workforce morale. By combining both quantitative and qualitative data, companies can develop a more rounded perspective on their distribution effectiveness, ensuring they are not only meeting targets but also maintaining high standards of service and employee engagement.
FAQS
What are the key safety protocols that should be implemented in a distribution centre?
Key safety protocols include regular safety training for employees, proper signage to indicate hazards, the use of personal protective equipment (PPE), and maintaining clear and unobstructed pathways to ensure safe movement within the facility.
How can distribution centres promote sustainable practices?
Distribution centres can promote sustainable practices by implementing energy-efficient technologies, reducing waste through recycling programmes, optimising transportation routes to lower emissions, and sourcing materials from environmentally responsible suppliers.
What performance metrics are most important for measuring success in distribution operations?
Important performance metrics include order accuracy, inventory turnover rate, delivery lead time, labour productivity, and overall operational efficiency. These metrics help identify areas for improvement and track the effectiveness of implemented practices.
How often should safety protocols be reviewed and updated?
Safety protocols should be reviewed at least annually or whenever there are significant changes in operations, equipment, or regulations. Regular audits and feedback from employees can also help identify the need for updates.
What role do KPIs play in optimising distribution centre operations?
KPIs serve as measurable indicators of performance that help managers assess the efficiency and effectiveness of distribution centre operations. They provide insights into performance trends, assist in setting operational goals, and enable data-driven decision-making.
Related Links
What to Consider When Designing a Distribution CentreHow to Optimise Distribution Centre Design for Efficiency
Roundup of Top Distribution Centre Design Innovations
Review of the Latest Distribution Centre Design Software
7 Key Features of an Efficient Distribution Centre
A Historical Overview of Distribution Centre Design Trends
Why You Should Consider Automated Solutions in Your Distribution Centre