How to optimise inventory management in warehouse operations
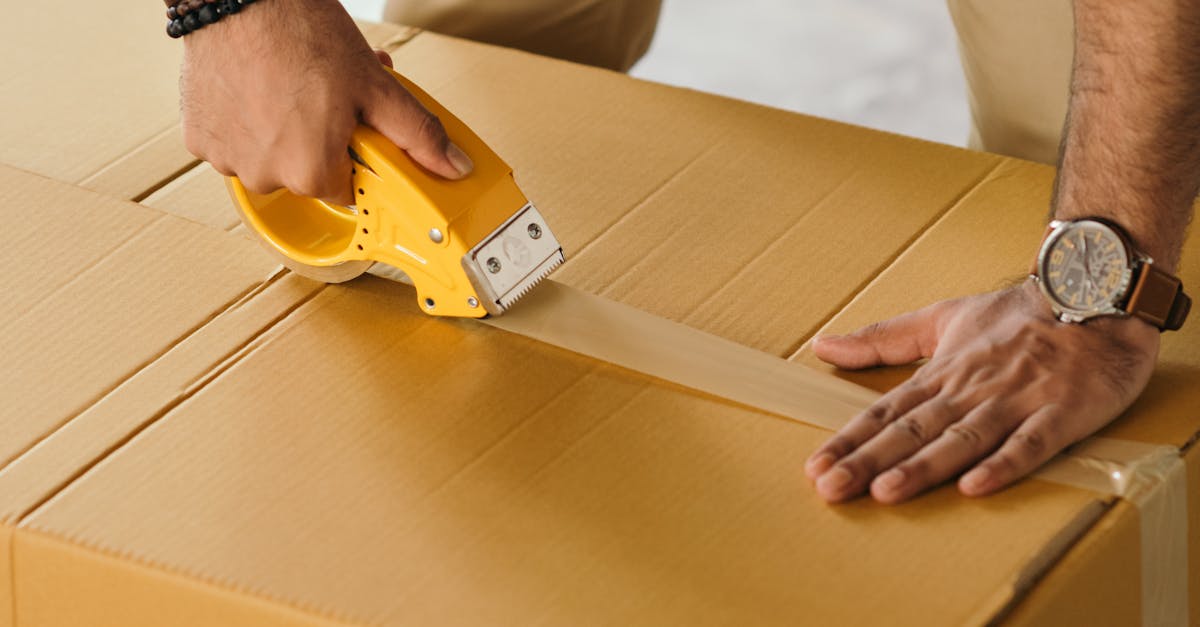
Setting Reorder Levels
Establishing appropriate reorder levels is essential for effective inventory management. This metric ensures that stock is replenished before it runs out, thereby minimising the risk of stockouts that could disrupt operations. To determine these levels, businesses should consider factors such as lead time, average sales velocity, and buffer stock requirements based on fluctuating demand patterns.
Accurate calculations for reorder levels rely on historical data and forecasts. Each product may have different characteristics that influence its turnover rate, so individual analysis is crucial. Regularly reviewing and adjusting these levels in response to changing market conditions or shifts in consumer behaviour can greatly enhance efficiency and optimise stock levels while reducing excess inventory.
Calculating Optimal Stock Levels for Products
Determining the appropriate stock levels for products is essential for maintaining operational efficiency. Businesses can achieve this balance by considering factors such as lead time, demand variability, and financial implications. Assessing historical sales data plays a vital role in forecasting future needs. By understanding past trends, companies can estimate how much stock to keep on hand, reducing the risk of overstocking or stockouts.
In addition to historical data, organisations should factor in seasonal fluctuations and promotional activities when calculating optimal inventory levels. Adjustments may be necessary based on supplier reliability and changes in customer preferences. Establishing a systematic approach to periodic review of stock levels ensures that products remain available to meet customer demands while minimising excess inventory costs. Accurate calculation ultimately supports smoother warehouse operations and enhances overall productivity.
Leveraging Data Analytics
Data analytics plays a crucial role in enhancing inventory management within warehouse operations. By harnessing the power of data, businesses can gain insights into inventory turnover rates, seasonal demand fluctuations, and product performance. Analysing past purchasing trends enables warehouses to forecast future demands more accurately, minimising excess stock and reducing instances of stockouts. This systematic approach aids in maintaining optimal stock levels, ensuring products are available when needed without overcommitting resources.
Furthermore, employing advanced analytics tools allows for the identification of patterns that may not be immediately apparent through traditional inventory practices. Sophisticated algorithms can evaluate large datasets, revealing which products are frequently sold together or determining the ideal reorder points based on historical data. As warehouses implement these insights into their operations, they can respond more quickly to changing customer preferences and market conditions. This proactive stance in inventory management not only reduces costs but also enhances overall operational efficiency.
Using Trends to Improve Inventory Decisions
Understanding market trends plays a crucial role in making informed inventory decisions. Historical sales data can reveal patterns in consumer behaviour, helping businesses anticipate fluctuations in demand. By analysing seasonal trends, holidays, and promotional events, companies can better align their stock levels with expected sales, thus minimising waste and ensuring that popular items are always available.
Additionally, leveraging technology enhances the ability to track these trends effectively. Advanced inventory management systems can integrate data from various sources, providing real-time insights into stock levels and product performance. This data-driven approach allows businesses to adjust their inventory strategy proactively. With a clear view of market dynamics, organisations can optimise their purchasing processes, selecting products that are more likely to sell based on current and predicted trends.
Training Staff on Inventory Procedures
Effective inventory management relies heavily on the skills and awareness of the staff involved in the process. Providing comprehensive training ensures that employees understand the importance of accurate stock levels and the impact of their actions on overall operations. Workshops and hands-on training sessions can help staff familiarise themselves with the inventory management system, enabling them to navigate the software and follow proper procedures with confidence. Knowledgeable staff members can identify inconsistencies and respond promptly, reducing potential losses and enhancing efficiency.
Regular training updates are equally crucial in keeping staff informed about new practices and technologies in inventory management. The warehouse environment is dynamic, with shifting product lines and changing market demands. Continued education on inventory procedures fosters a culture of adaptability among employees. Encouraging feedback from team members on the training process can also highlight areas for improvement and reinforce the importance of their roles in maintaining optimal inventory levels.
Importance of Employee Awareness and Skills
Understanding inventory procedures is crucial for all employees involved in warehouse operations. Knowledge of the processes enhances efficiency and reduces the likelihood of errors. When staff members are familiar with inventory management practices, they can accurately track stock levels, maintain appropriate reorder points, and prevent overstocking or stockouts. A well-informed workforce also contributes to better collaboration and communication, which are essential for smooth operations.
Training programs should incorporate practical sessions, ensuring that employees not only learn theoretical concepts but also gain hands-on experience. Regular workshops can reinforce skills and keep staff updated with the latest industry trends and technologies. Fostering a culture of continuous learning empowers employees and equips them to adapt to changing demands. This proactive approach leads to improved performance and a more resilient inventory management system.
FAQS
What are reorder levels in inventory management?
Reorder levels are predetermined stock levels that indicate when a new order should be placed to replenish inventory. This helps to prevent stockouts and ensures that products are available when needed.
How do I calculate optimal stock levels for products?
To calculate optimal stock levels, consider factors such as demand forecasting, lead times, storage capacity, and inventory turnover rates. Using data analytics can also aid in making more informed decisions regarding stock levels.
How can data analytics improve inventory management?
Data analytics can identify trends and patterns in inventory usage, helping to optimise stock levels, reduce waste, and enhance decision-making processes. It enables businesses to make data-driven predictions and adjustments to their inventory strategies.
Why is staff training important for inventory management?
Staff training is crucial as it ensures that employees are knowledgeable about inventory procedures, stock management systems, and best practices. This leads to greater efficiency, reduced errors, and improved overall performance in warehouse operations.
What should I include in staff training on inventory procedures?
Staff training should include topics such as inventory tracking methods, stocktaking procedures, understanding reorder levels, use of inventory management software, and the importance of accurate data entry to maintain optimal inventory levels.
Related Links
How to improve order fulfilment processesRoundup of trends in warehouse operations for 2024
Review of the latest automated warehousing technologies
10 best practices for effective order fulfilment
Historical developments in cold chain logistics
Why proper inventory management impacts overall efficiency