Why Logistics Performance Measurement is Crucial
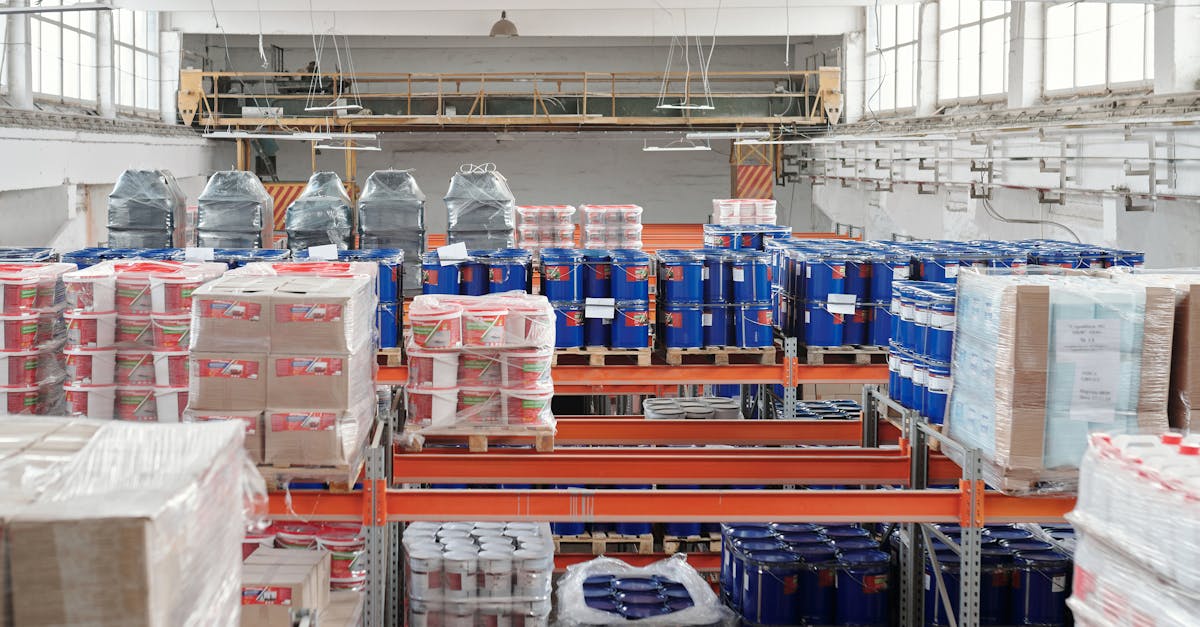
Benchmarking Against Industry Standards
Logistics companies often seek ways to improve efficiency and reduce costs. One effective method involves benchmarking their performance against established industry standards. This process helps organisations identify areas where they excel and where improvements are needed. It provides a framework to measure key performance indicators (KPIs) against competitors or best-in-class companies, enabling logistics firms to set realistic goals and track progress over time.
Adopting industry standards also promotes transparency and accountability within organisations. When logistics teams are aware of the benchmarks, they are more likely to strive for excellence. This awareness cultivates a competitive spirit and encourages continuous assessment of performance levels. Moreover, by regularly comparing their metrics with those of leading players in the market, companies can adapt strategies to stay relevant and competitive in an ever-evolving industry landscape.
The Importance of Comparative Analysis in Logistics
In the ever-evolving landscape of logistics, comparative analysis has emerged as a critical tool for organisations striving to enhance their operational efficiency. By evaluating performance metrics against those of industry peers, companies can identify areas of strength and pinpoint weaknesses within their supply chain processes. This analytical approach facilitates a deeper understanding of market dynamics and enables businesses to establish best practices, fostering a culture of continuous improvement.
Furthermore, benchmarking against established standards allows businesses to set realistic performance targets. Knowing where one stands in relation to competitors not only informs strategic planning but also encourages accountability within the organisation. Employees at all levels can become more motivated when they see their contributions directly impacting performance outcomes, leading to a more engaged workforce and ultimately, higher levels of customer satisfaction.
Technology and Logistics Performance Measurement
In recent years, technology has revolutionised the logistics industry, making performance measurement more precise and efficient. Advanced tools and software allow companies to track a wide array of metrics in real-time. These technologies facilitate comprehensive data collection, enabling organisations to analyse their performance against set benchmarks. Automation has reduced human error, providing more reliable data. Integrating systems such as transportation management systems (TMS) and warehouse management systems (WMS) optimises operations and generates insights that are crucial for strategic decision-making.
Data analytics plays a pivotal role in enhancing logistics performance measurement. Companies can harness big data analytics to gain deeper insights into their supply chain dynamics. By evaluating patterns and trends, businesses can identify inefficiencies and opportunities for cost savings. Predictive analytics further empower organisations to forecast demand accurately, ensuring that inventory levels are managed effectively. Investments in technology not only streamline operations but also foster a culture of data-driven decision-making, which underpins continuous improvement in logistics performance.
Leveraging Data Analytics for Improved DecisionMaking
Data analytics plays a pivotal role in optimising logistics operations. By harnessing vast amounts of data generated throughout the supply chain, companies can identify trends, inefficiencies, and potential areas for cost savings. Advanced analytics tools allow organisations to measure key performance indicators (KPIs) accurately, providing insights into delivery times, inventory levels, and transportation costs. This information enables businesses to make informed decisions backed by concrete evidence rather than relying solely on intuition or anecdotal experience.
The integration of predictive analytics further enhances decision-making capabilities. With the ability to forecast demand fluctuations and assess the impact of various logistical strategies, businesses can proactively address challenges before they escalate. By employing machine learning algorithms, organisations can refine their operational processes, enhance customer satisfaction, and position themselves ahead of competitors. Leveraging these insights fosters a responsive and agile logistics environment, crucial for maintaining a competitive edge in today’s fast-paced market.
Continuous Improvement in Logistics Operations
Logistics operations face constant pressure to enhance efficiency and reduce costs. Implementing a continuous improvement approach enables organisations to systematically identify and eliminate inefficiencies. By fostering a culture where employees at all levels are encouraged to contribute ideas, companies can tap into valuable insights that may otherwise remain overlooked. Regular training sessions and workshops can further empower staff, ensuring they are equipped with the latest skills and knowledge relevant to the industry.
Monitoring key performance indicators (KPIs) regularly is vital for assessing progress towards operational goals. This data-driven insight allows logistics managers to make informed decisions that align with strategic objectives. Establishing a framework for performance reviews ensures that improvements are not just one-off initiatives. Such reviews provide a structured opportunity to evaluate the effectiveness of changes implemented and to recalibrate strategies as necessary, driving ongoing optimisation in logistics operations.
Implementing a Culture of Performance Review
A shift towards a culture of performance review can significantly enhance logistics operations. Regular assessments empower teams to identify strengths and weaknesses in their processes. By fostering an environment where feedback is an integral part of daily activities, organisations can encourage employees to take ownership of their roles. This proactive approach often leads to innovative solutions and optimisation of resources.
Establishing a framework for performance evaluation requires commitment from all levels of the organisation. Leadership must advocate for transparency and open communication, ensuring that everyone is aligned with the performance metrics. Training sessions and workshops can also help equip employees with the necessary skills to engage effectively in reviews. Such initiatives facilitate a continuous loop of learning and improvement, ultimately contributing to a more agile logistics network.
FAQS
Why is logistics performance measurement important?
Logistics performance measurement is crucial as it enables companies to assess their operational efficiency, identify areas for improvement, and enhance overall supply chain effectiveness. It ensures that organisations can meet customer expectations while maintaining cost-efficiency.
How can benchmarking against industry standards benefit a logistics operation?
Benchmarking against industry standards helps logistics companies to evaluate their performance relative to peers, identify best practices, and set realistic performance targets. This comparative analysis facilitates strategic improvements and can lead to increased competitiveness in the market.
What role does technology play in logistics performance measurement?
Technology plays a significant role by providing tools for data collection, analysis, and reporting. Advanced software solutions and data analytics facilitate real-time tracking of performance metrics, enabling logistics managers to make informed decisions and optimise operations.
How can data analytics improve decision-making in logistics?
Data analytics allows for the examination of vast amounts of logistical data to uncover trends, patterns, and insights. By leveraging these insights, decision-makers can implement strategies that enhance efficiency, reduce costs, and improve service levels.
What is meant by implementing a culture of performance review in logistics operations?
Implementing a culture of performance review involves regularly evaluating and discussing performance metrics within the organisation. This fosters an environment of accountability and continuous improvement, encouraging employees to contribute to optimising logistics processes and achieving operational excellence.
Related Links
Why Demand Forecasting Fails in Some BusinessesWhat is Demand Forecasting and Its Importance
Roundup of Key Trends in Supply Chain Management
Review of Top Demand Forecasting Tools
10 Best Practices for Supplier Relationship Management
Historical Overview of Supply Chain Management Practices
What to Consider When Choosing Suppliers