How to Implement Efficient Picking Strategies
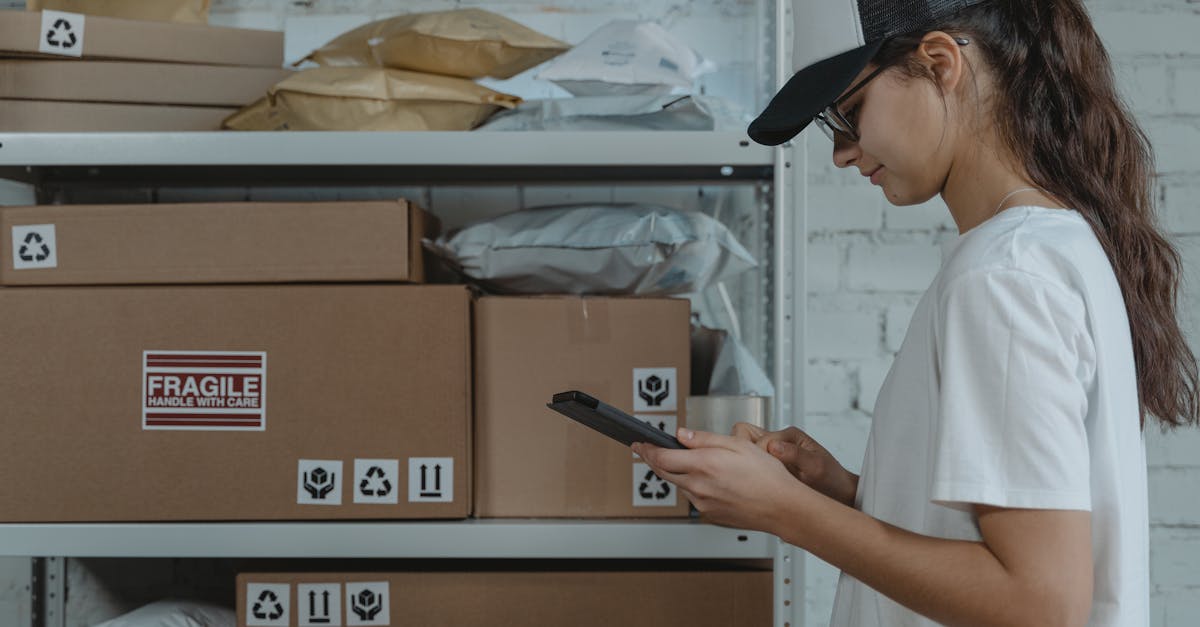
Implementing a RealTime Inventory System
The integration of a real-time inventory system can significantly enhance the efficiency of warehouse operations. By utilising technology to track stock levels, businesses can reduce the likelihood of overstocking or stockouts. RFID tags and barcode scanning can facilitate immediate updates to inventory records as products move in and out of the warehouse. This immediate visibility allows for better decision-making around order fulfilment and inventory reordering, ultimately leading to improved customer satisfaction.
Moreover, such systems can streamline communication between departments. Sales teams can access up-to-date inventory data, enabling them to provide accurate information to customers regarding product availability. Marketing initiatives can be better aligned with actual stock levels, helping to avoid promoting items that are not in supply. Additionally, real-time tracking supports inventory audits and helps identify discrepancies more swiftly, thereby contributing to the overall accuracy and reliability of inventory management practices.
Benefits of Inventory Management Software
Inventory management software plays a crucial role in streamlining operations within a warehouse. It automates numerous tasks, significantly reducing the time staff spend on manual data entry and inventory tracking. Enhanced accuracy in stock levels mitigates discrepancies that often lead to overstocking or stockouts. With real-time updates, teams can make informed decisions about purchasing and storage, ultimately contributing to increased efficiency.
Another advantage is the improved visibility it offers across the supply chain. Users can easily monitor stock movements, which aids in forecasting demand and planning for peak seasons. This helps businesses align their resources more effectively, minimising waste and optimising storage space. Additionally, the integration of analytics features allows companies to scrutinise past performance and identify trends, leading to more strategic decision-making in the future.
Measuring Picking Performance
Quantifying the efficiency of picking operations is essential for identifying areas for improvement. Various metrics can be employed to evaluate performance, including order accuracy, picking speed, and employee productivity. Assessing these metrics frequently can reveal patterns that inform better decision-making. For instance, tracking the number of items picked per hour may highlight training needs for individual staff members or indicate the necessity for optimised picking routes.
Additionally, utilising technology such as barcode scanners or mobile devices can contribute to more precise performance data. These tools help in capturing real-time information, ensuring accurate statistics for further analysis. By establishing a standard for measuring performance, businesses can create a baseline from which to enhance their picking processes. Regular review of these measurements fosters a culture of accountability, ultimately leading to improved operational efficiency.
Key Performance Indicators to Track
Establishing clear metrics is vital for assessing the effectiveness of picking operations. Some essential key performance indicators (KPIs) include order accuracy, which measures the percentage of correctly picked items compared to the total orders fulfilled. Tracking the average time taken per pick can also shed light on the efficiency of warehouse processes. Additionally, considering the rate of inventory turnover aids in understanding how quickly products are moving through the picking system.
Monitoring these KPIs enables warehouse managers to identify areas for improvement. A decline in accuracy may indicate a need for further training or adjustments to picking methods. Similarly, high turnover rates combined with low pick rates may suggest an imbalance in stock management or a shortage of staff. Regularly reviewing these indicators allows for informed decision-making, ultimately enhancing overall picking efficiency.
Continuous Improvement in Picking Processes
An effective picking process should adapt over time to incorporate new technologies and methodologies. Regularly reviewing existing workflows can unveil inefficiencies that may hinder productivity. Engaging employees in this evaluation often provides valuable insights, as they possess firsthand experience and ideas for improvement. Gathering their feedback creates an inclusive environment that fosters innovation and increases engagement.
The application of Lean principles is one approach to enhance picking operations. By minimising waste and streamlining processes, warehouses can achieve higher efficiency levels. Techniques such as 5S methodology help maintain organisation and cleanliness, which are essential for a productive workspace. Emphasising employee training on these principles will equip staff with the skills necessary for sustained improvement in picking performance.
Strategies for Ongoing Optimisation
To maintain a high level of efficiency in picking processes, businesses should regularly evaluate their operational workflows and identify areas for enhancement. Implementing lean principles can streamline operations by eliminating waste and optimising resources. Regular training sessions for staff not only improve skill sets but also reinforce best practices in picking techniques and order fulfilment. Integrating employee feedback into strategy adjustments can lead to practical improvements that enhance overall productivity.
Another effective approach involves investing in technology to automate and modernise picking strategies. Systems such as automated storage and retrieval systems (AS/RS) can drastically reduce time spent in the picking phase. In addition, employing mobile technologies enables real-time data capture, allowing for quicker access to inventory levels and order status. As trends in the industry evolve, continuously reassessing technology and methodologies ensures that operations stay ahead of the competition and adapt to changing market demands.
FAQS
What is a picking strategy in inventory management?
A picking strategy refers to the method used to retrieve products from inventory to fulfil customer orders efficiently. It involves determining the most effective way to organise and pick items based on factors like order volume, product types, and warehouse layout.
How can a real-time inventory system improve picking efficiency?
A real-time inventory system allows businesses to track stock levels and order fulfilment status instantly. This leads to better decision-making, reduced stock discrepancies, and faster order processing, ultimately enhancing the overall picking efficiency.
What are key performance indicators (KPIs) for measuring picking performance?
Key performance indicators for picking performance include order accuracy, picking speed, inventory turnover rate, and the number of items picked per hour. Tracking these metrics helps identify areas for improvement and measure the effectiveness of picking strategies.
What role does inventory management software play in optimising picking strategies?
Inventory management software streamlines operations by providing accurate stock data, automating order processing, and generating reports on picking performance. This enables businesses to implement more effective picking strategies and reduce errors during fulfilment.
How can businesses implement continuous improvement in their picking processes?
Businesses can implement continuous improvement by regularly reviewing their picking performance data, soliciting feedback from staff, testing new picking methods, and investing in training and technology. This approach fosters a culture of innovation and helps maintain an efficient picking operation.
Related Links
What to Know About Same-Day Delivery ServicesHow to Optimise Order Fulfilment Processes
Roundup of Top Trends in Order Fulfilment for 2024
Review of the Best Order Fulfilment Services in 2023
10 Tips for Improving Your Order Fulfilment Operation
History of Order Fulfilment in the Retail Industry