How to Optimise Order Fulfilment Processes
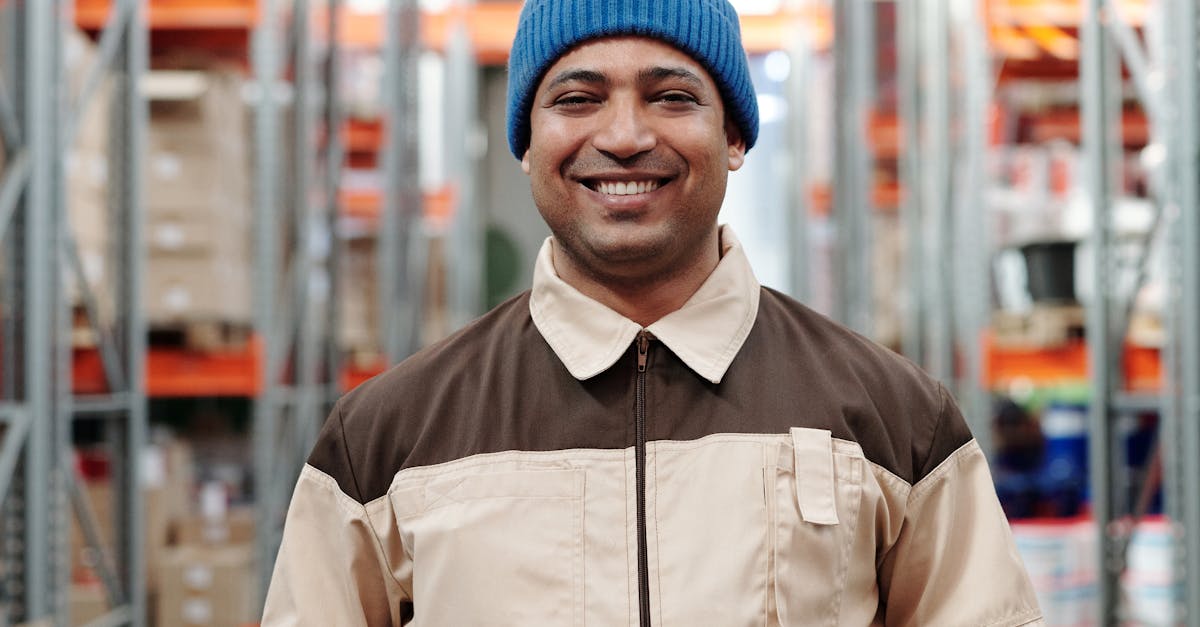
Training Staff for Better Performance
Training staff effectively is essential for enhancing their performance in order fulfilment processes. Comprehensive onboarding programmes should introduce employees to all operational procedures, ensuring they understand their roles and responsibilities. Continuous training sessions can prepare staff for any changes in technology or processes, allowing them to adapt quickly to new systems. Providing access to resources and ongoing support fosters a culture of learning and competence within the workforce.
Furthermore, engaging employees in hands-on activities enhances their practical understanding of the fulfilment process. Simulating real-life scenarios during training sessions can enhance problem-solving skills. Regular feedback encourages staff to identify areas for improvement and develop strategies to enhance efficiency. Recognising and rewarding employee achievements not only boosts morale but also motivates staff to maintain high performance in their roles.
Skills Development and Process Knowledge
Investing in staff training is essential for improving order fulfilment efficiency. Employees must have a deep understanding of the fulfilment process from start to finish. This knowledge enables them to identify potential issues early and streamline operations. Developing specific skills tailored to their roles can enhance their confidence and productivity. Regular workshops and hands-on training sessions can help staff stay updated on industry best practices and new technologies.
Process knowledge should extend beyond individual tasks. A comprehensive understanding of how various roles interlink creates a cohesive team environment. When team members grasp the overall order fulfilment workflow, they can better anticipate the needs of their colleagues and contribute to a smoother operation. This holistic approach not only boosts individual morale but also enhances team collaboration, ultimately benefiting the entire fulfilment process.
Communication with Suppliers
Effective communication with suppliers is vital for maintaining a smooth order fulfilment process. Clear dialogue can help clarify expectations and ensure that both parties are aligned on delivery timelines and product specifications. Regular updates and feedback loops can also pave the way for addressing potential issues before they escalate, minimising disruptions.
Building strong partnerships is essential in fostering a collaborative environment. Suppliers who feel valued are more likely to prioritise your orders and offer better support during peak times. Engaging in open discussions about challenges and providing constructive feedback can lead to improved performance on both sides, ultimately benefiting the overall supply chain.
Establishing Strong Partnerships
Building strong relationships with suppliers plays a crucial role in optimising order fulfilment processes. Trust is an essential element in these partnerships, as it encourages transparency and accountability. Regular communication helps suppliers understand demand fluctuations, enabling them to adjust their offerings accordingly. Collaborative forecasting can minimise stock shortages and reduce lead times, enhancing overall efficiency.
Investing time in nurturing these partnerships can yield significant benefits. Joint problem-solving initiatives often lead to innovation and improved processes. Suppliers who feel valued are more likely to prioritise your needs, ensuring timely delivery and quality assurance. Establishing a framework for regular feedback fosters continuous improvement, which ultimately leads to greater satisfaction for both parties involved.
Tracking and Monitoring Orders
The ability to track and monitor orders is essential for efficient order fulfilment. Implementing a robust tracking system allows businesses to gain visibility over their inventory and shipments, ensuring that they stay informed about the status of orders at all times. This transparency helps identify potential delays, enabling proactive communication with customers and adjustments to fulfilment strategies.
Utilising modern technology can significantly enhance this process. Inventory management software, alongside automated update alerts, provides real-time insights into stock levels, order processing, and delivery statuses. By integrating these tools, businesses can streamline their operations, reduce errors, and improve the overall customer experience. This comprehensive approach ensures that any issues can be swiftly addressed, maintaining the integrity of the order fulfilment process.
Tools for RealTime Updates
Effective order tracking relies heavily on modern technology. Real-time updates can significantly enhance visibility throughout the fulfilment process. Many companies employ tracking software that integrates with their existing systems. Such tools can provide immediate information about order status, including shipping progress and estimated delivery times. They help in minimising uncertainty and enable staff to respond swiftly to customer inquiries.
Utilising mobile applications has also become increasingly popular among businesses. These applications offer not only the ability to track orders but also the convenience of managing logistics on the go. Notifications about any delays or changes can be sent directly to users. This immediate communication is essential, allowing teams to make timely adjustments and keep customer experience at the forefront. Enhanced visibility through these tools ultimately leads to better customer satisfaction and improved operational efficiency.
FAQS
What is order fulfilment optimisation?
Order fulfilment optimisation involves streamlining and enhancing processes to ensure that orders are processed, packed, and delivered efficiently and accurately, ultimately improving customer satisfaction.
Why is staff training important in order fulfilment?
Staff training is crucial as it equips employees with the necessary skills and knowledge about processes, technology, and best practices, leading to better performance and reduced errors in order fulfilment.
How can I improve communication with my suppliers?
Improving communication with suppliers can be achieved by establishing regular check-ins, using collaborative tools, and fostering strong relationships that encourage transparency and responsiveness.
What tools can help with tracking and monitoring orders?
Various tools are available for tracking and monitoring orders, including inventory management software, order management systems, and real-time tracking applications that provide updates on shipment status.
How do strong partnerships with suppliers benefit order fulfilment?
Strong partnerships with suppliers can lead to better coordination, improved lead times, access to quality materials, and enhanced overall efficiency in the order fulfilment process.
Related Links
How to Implement Efficient Picking StrategiesRoundup of Top Trends in Order Fulfilment for 2024
Review of the Best Order Fulfilment Services in 2023
10 Tips for Improving Your Order Fulfilment Operation
History of Order Fulfilment in the Retail Industry
Why Order Fulfilment is Crucial for Customer Satisfaction