How to implement key performance indicators in logistics
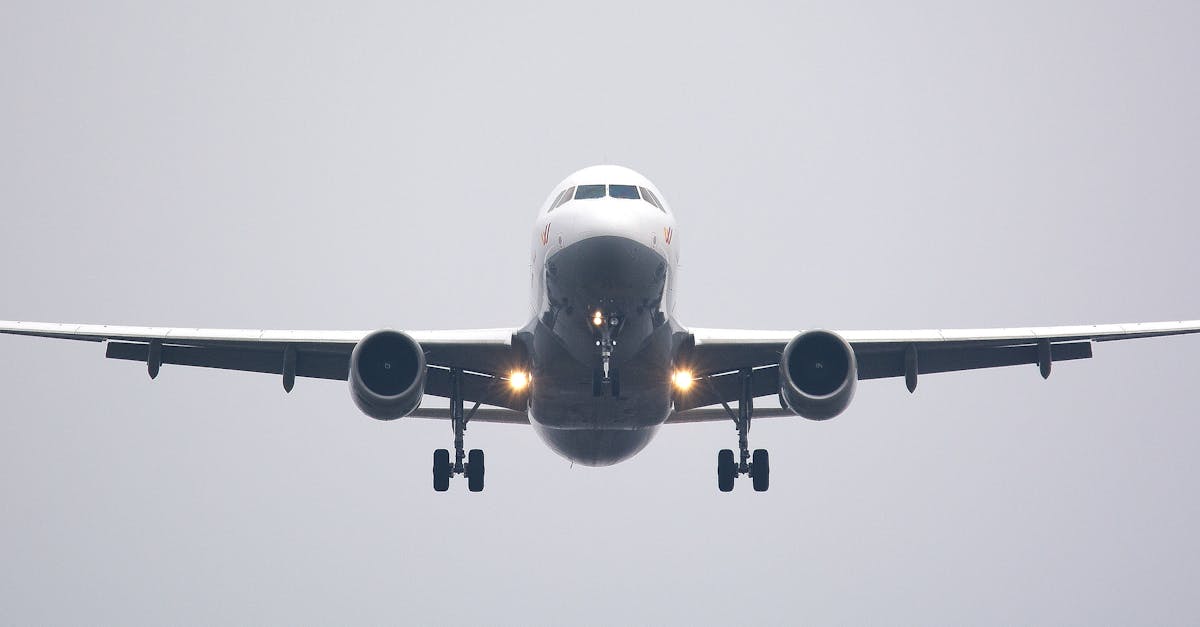
Establishing Baseline Measurements
Before implementing key performance indicators (KPIs) in logistics, it is crucial to gather accurate and relevant data to establish baseline measurements. This initial step provides a reference point against which future performance can be assessed. Data collection should encompass various aspects of logistics operations, such as delivery times, inventory levels, and transportation costs. Inaccuracy in this data can lead to misguided KPI targets, resulting in poor performance management.
Once baseline measurements are collected, they must be analysed to understand current operational performance. This analysis helps identify strengths and weaknesses within the logistics process. It is essential to document these findings, as they offer valuable insights for setting realistic and achievable KPI targets. Having a clear understanding of the baseline allows for better tracking of improvements and ensures that adjustments can be made based on actual performance outcomes.
Evaluating Current Performance Levels
Assessing performance levels begins with a comprehensive analysis of existing logistics processes. This evaluation should focus on key metrics such as delivery times, inventory turnover rates, and order accuracy. Gathering data from various sources, such as reports and feedback from stakeholders, is essential for a thorough understanding of how operations are currently functioning. Identifying trends and patterns in this data can help highlight areas requiring improvement and pinpoint strengths worth maintaining.
Furthermore, benchmarking against industry standards or competitors can provide valuable insights into performance levels. This comparative analysis establishes a clearer picture of where the organisation stands within the market context. It offers opportunities for identifying gaps in performance and setting realistic goals for improvement. By actively engaging with the data, organisations can foster a culture of continuous enhancement, motivating teams to strive for excellence and alignment with the overall business objectives.
Regularly Reviewing and Adjusting KPIs
Achieving optimal performance in logistics requires an ongoing commitment to monitoring and fine-tuning key performance indicators. Establishing a routine review process allows organisations to identify trends and patterns that may affect their logistics operations. This includes adjusting benchmarks based on evolving business goals, market conditions, or changes in customer demands. Regular evaluations ensure that KPIs remain relevant and effectively aligned with strategic objectives.
Flexibility remains a critical aspect of KPI management. As organisations encounter new challenges and opportunities, it is essential to adapt their KPIs accordingly. This adaptability can be facilitated by involving team members in the review process, ensuring that diverse perspectives are considered. Additionally, leveraging data analytics can provide deeper insights into performance metrics, allowing for more informed decisions when making adjustments to KPIs and their targets.
The Importance of Flexibility in KPI Management
Adapting key performance indicators to reflect the dynamic nature of the logistics industry is essential for sustained growth. Market conditions, customer expectations, and technological advancements can shift rapidly, necessitating a responsive approach to KPI management. Regular assessments help identify areas requiring adjustment while fostering an environment that embraces change. Rather than adhering rigidly to pre-established metrics, businesses should view KPIs as tools that assist in navigating the evolving landscape of logistics.
Flexibility in KPI management promotes a more holistic approach to performance evaluation. Engaging teams in the process of understanding and refining KPIs allows for greater ownership and accountability. Employees who believe their contributions shape key indicators are likely to take more initiative in their roles. This not only enhances job satisfaction but also aligns individual performance with broader organisational goals, driving the overall success of logistics operations.
Training Staff on KPI Significance
Understanding key performance indicators (KPIs) is crucial for every team member involved in logistics. Training staff on these metrics fosters a deeper comprehension of how their individual roles contribute to overall organisational success. A well-informed team can identify inefficiencies and work toward improvements. Workshops, online courses, and hands-on training sessions can help instil a strong understanding of KPIs, ensuring that employees recognise their importance in driving performance.
Moreover, promoting a culture of continuous learning regarding KPIs encourages employees to engage with the metrics on a personal level. When staff members see the direct impact of their actions on performance indicators, they are more likely to take ownership of their work. Recognising individual contributions can enhance morale and productivity. It is beneficial to incorporate regular discussions about KPIs into team meetings, fostering an environment where employees feel empowered to contribute to discussions about performance and improvement.
Enhancing Employee Awareness and Engagement
Creating a culture where employees understand the importance of key performance indicators (KPIs) in logistics can significantly enhance overall performance. This involves communicating the purpose and benefits of KPIs clearly. Training sessions, informational brochures, or workshops can serve as effective tools for educating staff. When employees comprehend how their individual roles contribute to broader business objectives, they tend to take greater ownership of their responsibilities.
Encouraging active participation in KPI discussions fosters a sense of involvement among employees. Recognising achievements and celebrating milestones related to KPI targets can further motivate staff. Regular feedback and open lines of communication about performance metrics are essential. When employees feel valued and understood, their commitment to the organisation's goals strengthens, creating a more productive work environment.
FAQS
What are key performance indicators (KPIs) in logistics?
Key performance indicators (KPIs) in logistics are measurable values that demonstrate how effectively a company is achieving its key business objectives. They help organisations assess their performance and guide operational decisions.
How do I establish baseline measurements for KPIs?
To establish baseline measurements for KPIs, begin by collecting historical data related to your logistics processes. This data will help you identify current performance levels, which you can then use as a foundation for setting realistic and achievable KPIs.
Why is it important to regularly review and adjust KPIs?
Regularly reviewing and adjusting KPIs is crucial because it allows organisations to remain responsive to changing market conditions, operational challenges, and business goals. This flexibility ensures that KPIs remain relevant and continue to drive performance improvements.
How can I train staff on the significance of KPIs?
Training staff on the significance of KPIs can be achieved through workshops, seminars, and hands-on training sessions. It's important to communicate how KPIs relate to their individual roles and the overall success of the organisation, fostering a culture of accountability and engagement.
What is the importance of flexibility in KPI management?
Flexibility in KPI management is important because it enables organisations to adapt their performance measures to reflect changing business strategies, customer demands, and operational challenges. This adaptability ensures that KPIs remain aligned with the organisation's goals and promote continuous improvement.
Related Links
What to consider for effective logistics performance measurementHow to optimise logistics performance measurement
Roundup of best practices for logistics performance evaluation
Review of top logistics performance measurement tools
7 essential metrics for logistics performance measurement
Why logistics performance measurement is crucial for success