How to Optimise Inventory Management for Maximum Efficiency
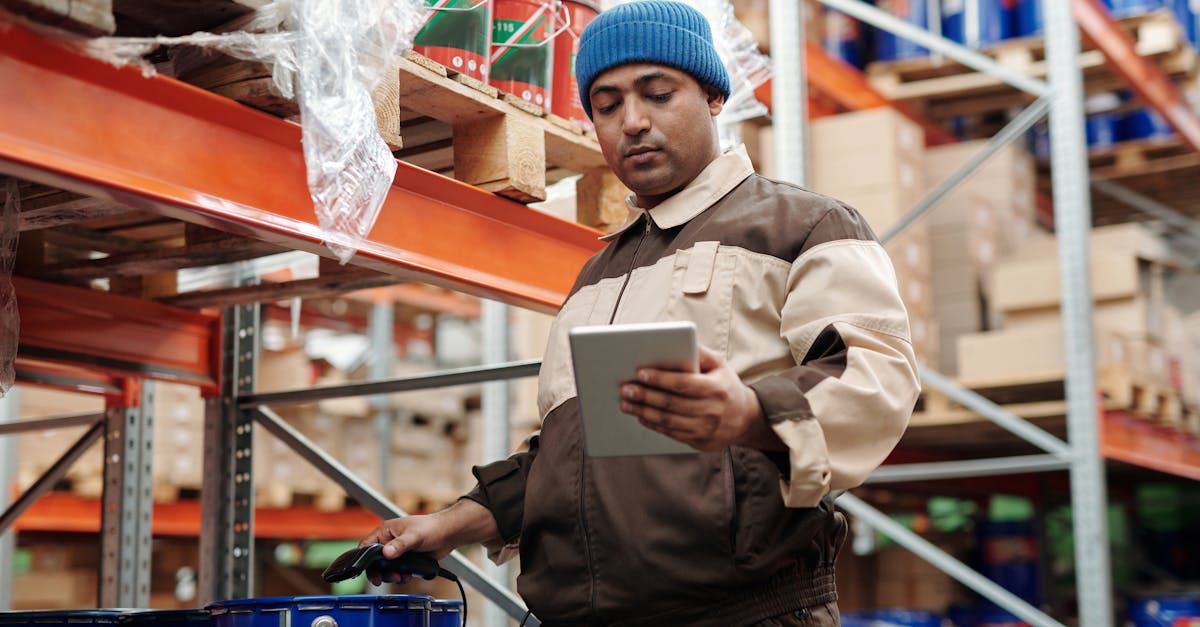
Categorising Inventory Effectively
Effective categorisation of inventory plays a crucial role in optimising management processes. By sorting products into distinct groups, businesses can gain clarity on stock levels and streamline operations. Common categorisation methods vary, but they often involve grouping items based on criteria such as turnover rates, value, or physical characteristics. This approach allows companies to allocate resources more efficiently and focus on what truly matters in their inventory.
Using categorisation, businesses can identify fast-moving items and allocate space in a manner that enhances retrieval speed. Categories can also aid communication across teams, ensuring everyone involved understands the status and location of inventory. With accessible and well-organised inventory data, companies can make informed decisions, reduce holding costs, and improve overall productivity.
The ABC Analysis Method
In inventory management, categorising stock according to its importance can significantly enhance efficiency. The ABC analysis method divides inventory into three categories: A, B, and C. A items represent the most valuable products, typically constituting a small percentage of total inventory but accounting for a large portion of overall value. B items are of moderate value, while C items, although numerous, contribute least to total value. This hierarchical approach helps businesses prioritise their management efforts and focus resources where they matter most.
By adopting the ABC analysis method, organisations can optimise their inventory control processes. Regularly reviewing stock classifications allows for better forecasting and aids in identifying trends in demand. Proper management of A items ensures that critical stock levels are maintained, preventing stockouts that can disrupt operations. Conversely, it encourages the efficient handling of C items, reducing excess holding costs and freeing up capital for more impactful investments. This systematic categorisation underpins a more strategic approach to inventory management.
Streamlining Supply Chain Processes
Efficient supply chain processes are essential for minimising delays and ensuring that inventory levels are accurately maintained. Companies should consider implementing advanced technology solutions to automate elements of their supply chain. This can include inventory management systems that provide real-time data on stock levels, order statuses, and demand forecasts. Additionally, leveraging analytics can help identify bottlenecks and areas for improvement, allowing businesses to make informed decisions that enhance operational efficiency.
Collaboration with suppliers is another crucial aspect of optimising supply chain processes. Establishing strong relationships can lead to better communication and understanding of each other's capabilities and constraints. Regular meetings and updates can facilitate transparency, making it easier to adjust orders based on current demand and production schedules. This proactive approach can significantly reduce lead times and improve the responsiveness of the overall supply chain.
Collaborating with Suppliers for Efficiency
Building strong relationships with suppliers can significantly enhance inventory management. Open communication encourages transparency regarding stock levels and lead times. When suppliers are well-informed about order patterns and demand forecasts, they can adjust production schedules accordingly. This proactive collaboration can help mitigate delays and prevent stockouts, ensuring that inventory levels align closely with business needs.
Establishing regular meetings or check-ins with suppliers fosters a deeper understanding of each party's capabilities and limitations. Suppliers can provide valuable insights into market trends or potential challenges that may arise. These discussions pave the way for joint problem-solving and the identification of opportunities for optimising processes. By working closely together, businesses can not only improve efficiency but also adapt more swiftly to changes in demand or supply chain disruptions.
Conducting Regular Inventory Audits
Regular inventory audits play a crucial role in maintaining the accuracy of stock levels and ensuring that financial records reflect the true value of assets. These assessments help identify discrepancies between physical stock and what is recorded in the inventory management system. By implementing a consistent schedule for these audits, businesses can uncover issues such as theft, loss, or administrative errors. Moreover, regular reviews support timely decision-making regarding reordering and obsolescence.
Employing various methods for stocktaking can enhance the auditing process. Cycle counting is one approach that allows for a portion of the inventory to be counted on a regular basis, reducing disruption and maintaining continuous operations. By training staff in effective auditing practices, businesses can foster a culture of accountability and accuracy. In addition, leveraging technology, such as barcode scanners or RFID systems, can streamline the auditing process, minimising human error and improving efficiency in tracking inventory levels.
Best Practices for Stocktaking
Accurate stocktaking is essential for maintaining a well-organised inventory system. Implementing a consistent schedule for audits can prevent discrepancies and ensure that records reflect actual stock levels. Utilising technology, such as barcode scanners or inventory management software, can greatly enhance the efficiency of the stocktaking process. Training staff in proper stocktaking techniques is also crucial, as familiarity with procedures reduces errors and improves overall accuracy.
Establishing a clear methodology can further optimise stocktaking efforts. Dividing inventory into manageable sections may facilitate easier counting and reduce the likelihood of oversight. Physical counts should be conducted in a quiet environment, allowing staff to focus on their task without distractions. Regular reviews of stock movement alongside physical counts also provide insights into underlying issues, helping to identify slow-moving items or potential stock losses.
FAQS
What is the ABC analysis method in inventory management?
The ABC analysis method categorises inventory into three classes (A, B, and C) based on their importance, helping businesses prioritise the management of high-value items.
How can I collaborate with suppliers to improve inventory efficiency?
Collaborating with suppliers can involve sharing sales forecasts, setting up reorder alerts, and establishing clear communication channels to ensure timely delivery and reduce excess stock.
Why are regular inventory audits important?
Regular inventory audits help identify discrepancies between recorded and actual stock levels, allowing businesses to maintain accuracy, reduce shrinkage, and optimise ordering processes.
What are some best practices for effective stocktaking?
Best practices for stocktaking include conducting audits at regular intervals, using technology to automate the process, training staff appropriately, and ensuring a systematic approach to counting and recording inventory.
How can categorising inventory effectively lead to better management?
Effective categorisation of inventory allows businesses to focus their resources on managing the most critical items, improves decision-making regarding stock levels, and enhances overall efficiency in inventory management.
Related Links
How to Develop an Effective Supply Chain StrategyRoundup of Key Trends in Supply Chain Strategy
10 Best Practices for Effective Inventory Management
Historical Evolution of Supply Chain Management
Review of Top Demand Forecasting Tools
Why Supply Chain Strategy Matters in Today's Market
Why Logistics Performance Measurement is Crucial for Success