Roundup of innovative trends in warehouse operations
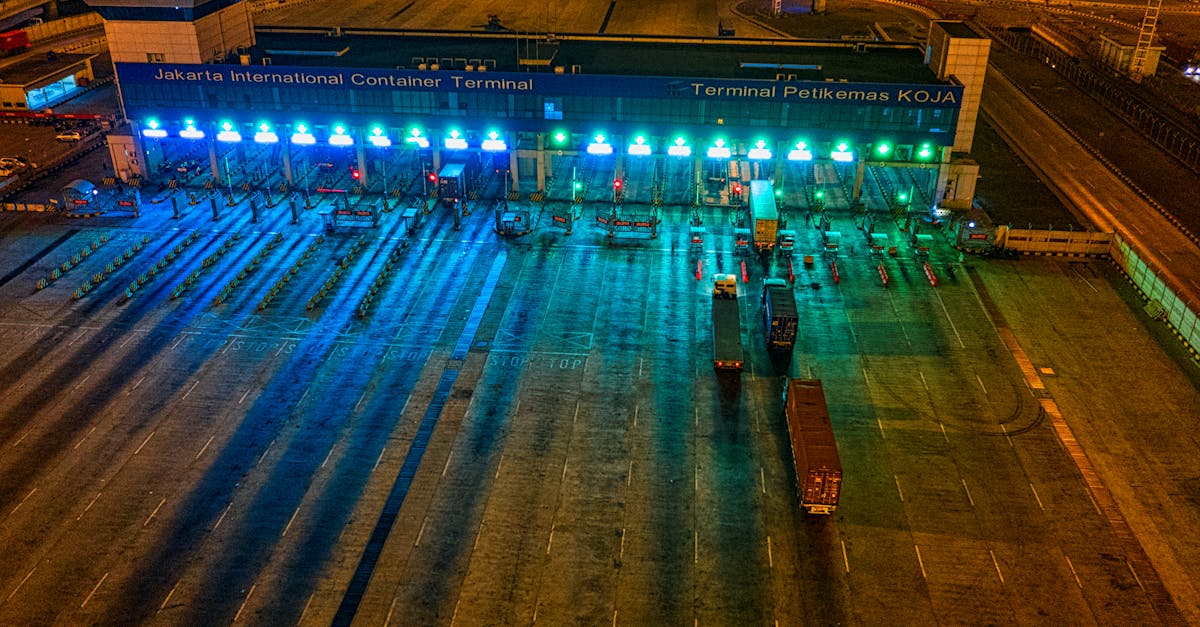
Flexible Warehouse Designs
The modern warehouse landscape demands adaptability in its design to accommodate fluctuating inventory levels and shifting consumer preferences. Innovative layouts, including moveable shelving and modular racking systems, allow operators to modify their storage configurations as needed. This flexibility not only maximises space efficiency but also enhances operational workflow. Implementing dynamic designs can significantly reduce downtime, ensuring that warehouses remain responsive to market changes.
Integrating technology into warehouse design fosters a more fluid operation. Automated guided vehicles and drones are increasingly becoming integral parts of innovative setups, offering streamlined pick-and-pack procedures. These technologies facilitate quicker responses to orders while reducing manual handling. The result is a more efficient environment that can support a variety of tasks and improve overall productivity.
Adapting Layouts for Changing Needs
Modern warehouses require adaptability in design to keep pace with evolving business demands. Traditional fixed layouts often struggle to accommodate shifts in product volume, variety, and order patterns. As logistics become increasingly dynamic, the ability to rearrange shelving, storage areas, and workstation configurations is crucial. Flexible designs can optimise space utilisation and improve workflow efficiency, ultimately leading to reduced operational costs.
Utilising modular systems allows for quick adjustments in layout without extensive downtime. Incorporating movable shelving units and adjustable racking systems supports real-time changes based on inventory requirements. These innovative strategies enable warehouses to respond swiftly to market fluctuations while maintaining high levels of productivity. Investing in adaptable designs helps facilities stay competitive amid constant shifts in consumer behaviour and supply chain dynamics.
Advanced Inventory Tracking Systems
The transformation of inventory management has taken a significant leap forward, particularly with the integration of advanced technology. Companies are increasingly turning to automated systems that provide real-time visibility of stock levels. This approach not only minimises human error but also enhances the efficiency of warehouse operations. With data being processed and analysed quickly, businesses can adjust their inventory needs dynamically, reducing waste and optimising storage space.
Utilising sophisticated tracking systems improves accuracy in inventory counts and enhances order fulfilment processes. One notable innovation involves the use of RFID technology, which allows for seamless tracking of goods throughout the supply chain. This technology enables automatic logging of items as they move in and out of the warehouse, simplifying the reconciliation of inventory records. Moreover, the ability to monitor stock levels from any location empowers managers to respond promptly to needs and maintain an agile operation.
Utilising RFID Technology
Radio-Frequency Identification (RFID) technology is revolutionising inventory management in warehouses. This system allows for the automatic identification and tracking of items using electromagnetic fields. Manufacturers and retailers benefit from enhanced accuracy in inventory data, reducing human error and increasing efficiency during stock assessments. With RFID tags affixed to products, warehouses can achieve real-time visibility of their stock, leading to more informed decision-making.
The integration of RFID technology streamlines the entire supply chain process. It enables faster check-in and check-out, while systems can effectively track the movement of goods within the warehouse. By implementing this technology, companies can optimise their storage capabilities and improve order fulfilment rates. As a result, businesses are able to respond more swiftly to changes in demand, thereby enhancing overall operational effectiveness.
Employee Training and Development
The evolving landscape of warehouse operations necessitates a committed focus on employee training and development. As organisations embrace new technologies and methodologies, workers must be equipped with the skills to navigate these changes effectively. Training programmes that emphasise hands-on experience, coupled with theoretical knowledge, can significantly enhance employee competence. Incorporating simulations and real-world scenarios into training helps employees gain confidence in their abilities, ensuring they are ready to meet the challenges of a dynamic warehouse environment.
Investing in ongoing upskilling also fosters a culture of continuous improvement within the workforce. Encouraging employees to take advantage of professional development initiatives not only boosts morale but also enhances overall productivity. A robust training framework can address skills gaps and prepare teams for future technological advancements, ensuring the workforce remains agile and adaptable. Such proactive approaches help organisations stay competitive while also creating a more engaged and capable workforce.
Upskilling for Future Challenges
The rapid evolution of technology in warehouse operations necessitates a workforce skilled in various new tools and methodologies. Training programmes focusing on areas such as robotics and automation ensure that employees remain proficient in managing advanced systems. Additionally, offering workshops on problem-solving and critical thinking fosters a proactive approach to dealing with unexpected challenges that may arise in day-to-day operations.
Integrating ongoing educational initiatives within the workplace proves essential for maintaining a competitive edge. Companies that invest in their staff's professional development cultivate a more adaptable workforce capable of embracing change. As new technologies continue to reshape industry standards, a commitment to continuous learning becomes imperative for both employee satisfaction and operational efficiency.
FAQS
What are flexible warehouse designs?
Flexible warehouse designs refer to adaptable layouts that can be modified to accommodate changing operational needs, such as varying inventory levels or shifting product lines.
How can adapting layouts benefit warehouse operations?
Adapting layouts can optimise space utilisation, improve workflow efficiency, and enhance overall productivity by allowing for quicker adjustments to meet demand fluctuations.
What are advanced inventory tracking systems?
Advanced inventory tracking systems are technologies and methodologies that enhance the monitoring and management of stock levels, locations, and movements within a warehouse, ensuring accuracy and efficiency.
How does RFID technology improve inventory tracking?
RFID (Radio Frequency Identification) technology improves inventory tracking by allowing for real-time monitoring of items using radio waves, significantly reducing manual errors and increasing inventory visibility.
Why is employee training important in warehouse operations?
Employee training is crucial in warehouse operations as it equips staff with the skills and knowledge necessary to use new technologies effectively, adapt to innovative processes, and ensure safety standards are met.
Related Links
Review of top automated warehousing systems on the marketHow to implement an effective order fulfilment strategy
7 best practices for efficient order fulfilment
History of inventory management techniques
Why cold chain logistics is critical for perishable goods
Why automated warehousing systems are essential for modern logistics
What to consider when designing a distribution centre