How to implement an effective order fulfilment strategy
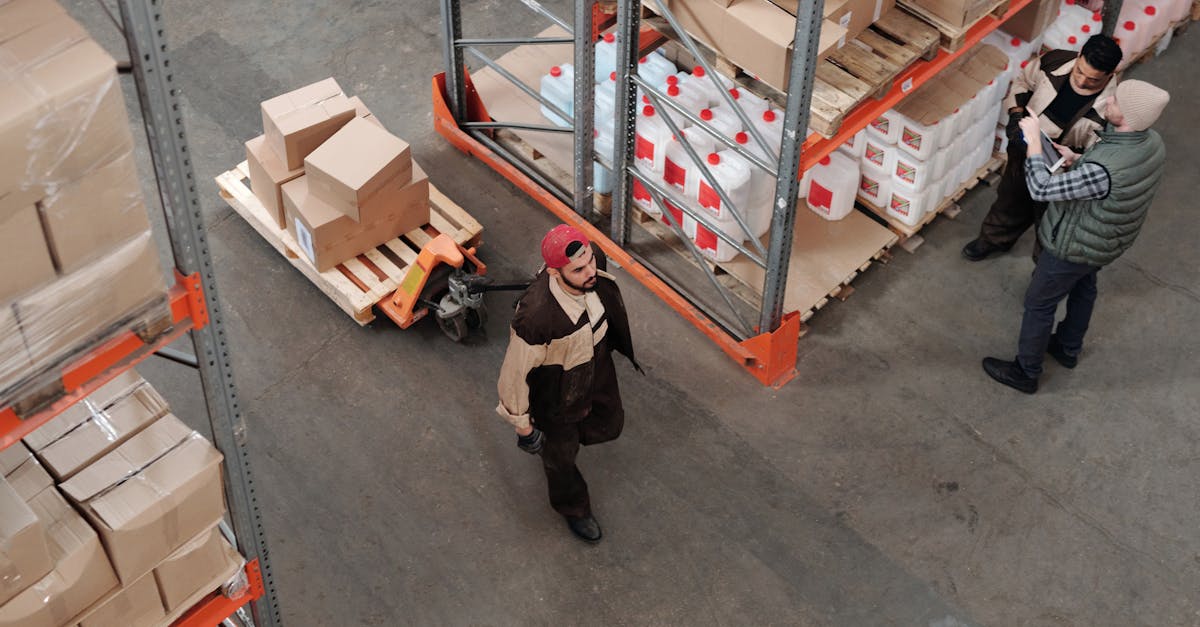
Implementing Efficient Order Processing Systems
An effective order processing system is crucial for maintaining customer satisfaction and operational efficiency. Integrating a robust software solution can streamline workflows, minimise human error and ensure that orders are processed in a timely manner. Clear visibility into the status of orders helps staff manage workloads effectively and address potential issues before they escalate. Automation of repetitive tasks allows employees to focus on more strategic activities, ultimately enhancing overall productivity.
Training employees on the new systems is equally important to maximise the effectiveness of the implementation. Comprehensive training programmes not only empower staff to use the technology proficiently but also foster an environment of continuous improvement. Regular feedback loops among team members can identify areas for enhancement, ensuring the system evolves to meet changing demands. By prioritising these steps, businesses can establish a strong foundation for a responsive order processing system.
Leveraging Technology for Automation
Automation plays a crucial role in streamlining order fulfilment processes. By integrating warehouse management systems and inventory control software, businesses can efficiently track stock levels, manage orders, and predict demand trends. These technologies reduce manual intervention, thereby minimising errors and improving overall accuracy in order processing. Additionally, employing barcode scanning and RFID technology enhances inventory visibility. With real-time data, companies can swiftly respond to fluctuations in supply and demand.
Robotic solutions are increasingly being adopted within warehouses to optimise picking and packing operations. Automated guided vehicles can transport products from one location to another, freeing up staff for more complex tasks. Installation of advanced software systems allows for better routing and scheduling, ensuring timely deliveries. Such innovations not only heighten operational efficiency but also contribute to higher customer satisfaction levels through quicker response times and improved service quality.
Enhancing Packaging and Shipping Methods
Optimising packaging and shipping methods can significantly impact both customer satisfaction and operational efficiency. Choosing the right materials is crucial for protecting products during transit without adding unnecessary weight. Lighter packaging can reduce shipping costs while maintaining adequate protection. Eco-friendly options are becoming increasingly popular, appealing to environmentally conscious consumers and helping companies align with sustainability goals.
Implementing efficient shipping processes is equally important. For instance, evaluating shipping carriers based on their delivery times, reliability, and costs allows businesses to select the best options for their needs. Tracking systems enhance visibility for both the company and the customer throughout the delivery process. This not only fosters trust but also reduces the likelihood of customer complaints regarding lost or delayed packages.
Selecting Materials for Cost Efficiency and Safety
Choosing the right materials is essential not only for cost efficiency but also for ensuring the safety of products during transit. Lightweight materials can reduce shipping costs, yet they must still provide adequate protection. Consider using packaging solutions like biodegradable alternatives or recycled options that align with sustainability goals. Such materials can enhance brand image while appealing to environmentally conscious consumers.
Safety is a critical component of packaging design. Selecting materials that meet industry safety standards can prevent damage to products and ensure customer satisfaction. Additionally, incorporating tamper-evident features can further secure packaged goods, providing peace of mind to both businesses and customers. Evaluating materials based on performance characteristics, environmental impact, and cost will lead to more informed choices.
Fostering Strong Supplier Relationships
Strong supplier relationships are fundamental to an effective order fulfilment strategy. Establishing connections built on trust and respect can help ensure a reliable supply chain. When suppliers feel valued, they are more likely to prioritise your orders and offer better terms. Regular engagement through meetings and feedback can strengthen these ties, creating a partnership where both parties understand each other's needs and challenges. This interaction leads to greater transparency, facilitating adjustments in supply based on market demands.
Open communication channels are essential for nurturing these relationships. Timely updates about changes in order volumes or emerging trends help suppliers align their resources accordingly. This proactive approach enables the identification of potential bottlenecks before they escalate into issues. Moreover, maintaining clear lines of communication fosters collaboration, which can lead to innovations in product offerings and service delivery. By working together, businesses and suppliers can adapt to shifts in the market more effectively, enhancing overall fulfilment strategies.
Establishing Open Communication Channels
Clear communication is vital in any supply chain. Engaging in regular dialogues with suppliers can uncover potential issues before they escalate. Sharing forecasts and expectations enables suppliers to align their capabilities with order demands. This proactive approach fosters a sense of partnership, which can lead to improved responsiveness and flexibility.
Utilising various communication tools can enhance the flow of information. Email, instant messaging, and regular video conferences can facilitate timely updates on order status and shipping schedules. Creating a centralised platform for updates allows both parties to track changes effectively. This transparency strengthens trust and ultimately contributes to a more efficient fulfilment process.
FAQS
What is an order fulfilment strategy?
An order fulfilment strategy is a systematic approach that businesses use to manage the entire process of receiving, processing, and delivering customer orders efficiently and effectively.
How can technology improve order fulfilment?
Technology can enhance order fulfilment by automating processes such as inventory management, order tracking, and shipping logistics, which reduces errors and speeds up the overall fulfilment process.
Why is packaging important in the order fulfilment process?
Packaging is crucial as it protects products during transit, ensures they arrive in good condition, and can also impact the unboxing experience for customers, influencing their overall satisfaction.
What role do suppliers play in order fulfilment?
Suppliers are essential as they provide the necessary products and materials for order fulfilment. Strong relationships with suppliers enhance reliability, reduce lead times, and can lead to better pricing.
How can open communication improve supplier relationships?
Open communication fosters trust and transparency, allowing for quicker problem resolution, better alignment on expectations, and the ability to adapt to changes in demand or supply chain disruptions.
Related Links
How to optimise inventory management in warehousesRoundup of innovative trends in warehouse operations
Review of top automated warehousing systems on the market
7 best practices for efficient order fulfilment
History of inventory management techniques
Why cold chain logistics is critical for perishable goods
Why automated warehousing systems are essential for modern logistics