How to optimise inventory management in warehouses
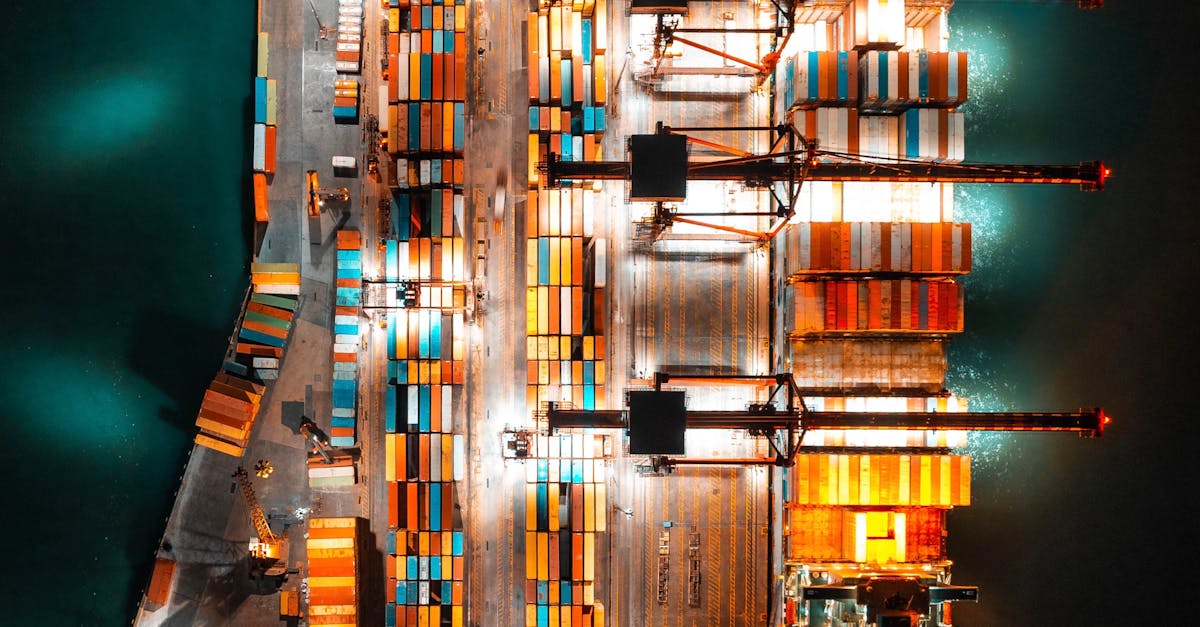
Establishing Reorder Points
Reorder points are essential in maintaining optimal inventory levels. They indicate the moment inventory should be replenished to prevent stockouts while minimising excess stock. Establishing these points requires a thorough analysis of sales patterns, lead times, and the variability in demand. Accurate data is vital to determine when to reorder items, ensuring that operations continue smoothly.
Monitoring these points regularly is crucial for adapting to changes in demand or supply chain dynamics. An organisation might find that seasonal fluctuations affect sales, necessitating adjustments to reorder points. Furthermore, incorporating technology such as inventory management software can streamline this process. These systems can automatically calculate reorder points based on real-time data, helping to enhance efficiency and reduce the likelihood of human error.
Calculating Optimal Stock Levels
Determining the right amount of stock to maintain is critical to effective inventory management. This involves analysing historical sales data, understanding seasonal trends, and considering lead times from suppliers. By evaluating this information, businesses can establish a baseline that reflects both regular demand and any anticipated fluctuations. Utilising methods such as the Economic Order Quantity (EOQ) model can help strike a balance between ordering costs and holding costs, guiding businesses in making informed purchasing decisions.
In addition to historical data, integrating advanced forecasting techniques can enhance the accuracy of stock level calculations. Utilising software tools that automate data analysis allows for real-time insights into inventory needs. Regularly reviewing these optimal stock levels keeps operations responsive to changing market conditions. Adjustments may be necessary as consumer behaviour shifts or unforeseen events arise, ensuring inventory management remains both effective and efficient.
Conducting Regular Inventory Audits
Inventory audits play a vital role in maintaining accuracy within warehouse stock levels. Regularly scheduled audits can help identify discrepancies between what is physically present and what is recorded in inventory systems. This practice not only assures the integrity of stock data but also highlights potential issues in the supply chain, such as theft or administrative errors. By systematically checking inventory, businesses can enhance accountability and foster a culture of precision, which ultimately supports inventory optimisation.
There are several types of audits that warehouses can implement, each offering unique benefits. Physical inventory counts, cycle counting, and perpetual inventory checks all serve to ensure that records align with actual stock levels. Each method varies in frequency and intensity, allowing organisations to choose an approach that fits their operational needs. Regular oversight through these audits diminishes the risk of stockouts and overstock situations, which can lead to increased costs and reduced customer satisfaction. A structured audit process not only safeguards assets but also empowers businesses to make informed decisions based on reliable data.
Types of Audits and Their Benefits
Regularly scheduled audits play a crucial role in maintaining accurate inventory counts. There are various types of audits, including cycle counts, full-count reviews, and spot checks. Cycle counts involve counting a subset of inventory on a regular basis, allowing for errors to be identified and corrected before they impact broader operations. Full-count reviews are comprehensive and typically conducted annually, providing a complete snapshot of inventory status. Spot checks focus on specific high-value or fast-moving items, ensuring their accuracy without requiring a full-scale audit. Each method has its place in a robust inventory management strategy.
Implementing these auditing techniques brings numerous benefits to a warehouse operation. First, they help identify discrepancies between recorded and actual inventory, reducing overstock or stockout situations. Moreover, regular audits foster accountability among staff, as individuals become responsible for monitoring specific areas of stock. This practice not only improves accuracy but also contributes to overall efficiency in the supply chain. Enhanced inventory accuracy, streamlined operations, and improved employee engagement are just a few of the advantages derived from conducting regular audits.
Training Staff on Inventory Processes
Proper training for staff on inventory processes is vital for any warehouse operation. Employees need to be well-versed in the systems and technologies used for tracking stock levels and managing orders. Hands-on training sessions can provide practical experience while instructional materials can serve as a reference. Understanding the importance of accuracy in inventory management can significantly reduce discrepancies and improve overall efficiency.
Engaging employees in the inventory process fosters a sense of responsibility and ownership. Regular training updates help keep staff informed about any changes in procedures or technologies. This ongoing education not only enhances skill sets but also encourages a proactive approach to inventory management. A well-informed workforce contributes to smoother operations and better decision-making, ultimately leading to a more efficient warehouse environment.
Importance of Employee Engagement
Engaging employees in inventory management processes fosters a sense of ownership and responsibility. When staff understand their role in optimising inventory usage and tracking stock levels, they become more invested in achieving organisational goals. Regular training sessions can highlight the importance of their contributions, leading to better performance and reduced errors during stocktakes.
Moreover, encouraging feedback from employees can provide valuable insights into potential inefficiencies within the system. Creating an environment where team members feel comfortable sharing their ideas can lead to innovative solutions for inventory challenges. This collaboration not only improves operational efficiency but also enhances employee morale, which contributes to a more cohesive work atmosphere.
FAQS
What is a reorder point in inventory management?
A reorder point is the specific stock level at which new inventory should be ordered to prevent stockouts. It helps ensure that products are replenished in a timely manner, based on sales velocity and lead times.
How do I calculate optimal stock levels for my warehouse?
To calculate optimal stock levels, consider factors such as demand forecasting, lead time from suppliers, storage capacity, and safety stock requirements. This involves analysing historical sales data and trends to determine the appropriate amount of inventory to maintain.
What are the benefits of conducting regular inventory audits?
Regular inventory audits help identify discrepancies between physical stock and recorded inventory, improve accuracy in stock levels, prevent theft and shrinkage, and optimise inventory turnover. They also enhance overall inventory management efficiency.
What types of inventory audits can I conduct?
There are several types of inventory audits, including physical counts, cycle counting, and perpetual inventory audits. Each type has its benefits; for instance, physical counts provide a comprehensive overview, while cycle counting allows for continuous monitoring without halting operations.
Why is training staff on inventory processes important?
Training staff on inventory processes is crucial as it ensures that employees understand the best practices for managing stock, using inventory management systems, and following company protocols. This engagement can lead to greater accuracy, efficiency, and a reduction in errors in inventory handling.
Related Links
What is inventory management and why is it importantHow to implement an effective order fulfilment strategy
Roundup of innovative trends in warehouse operations
Review of top automated warehousing systems on the market
7 best practices for efficient order fulfilment
History of inventory management techniques