What is inventory management and why is it important
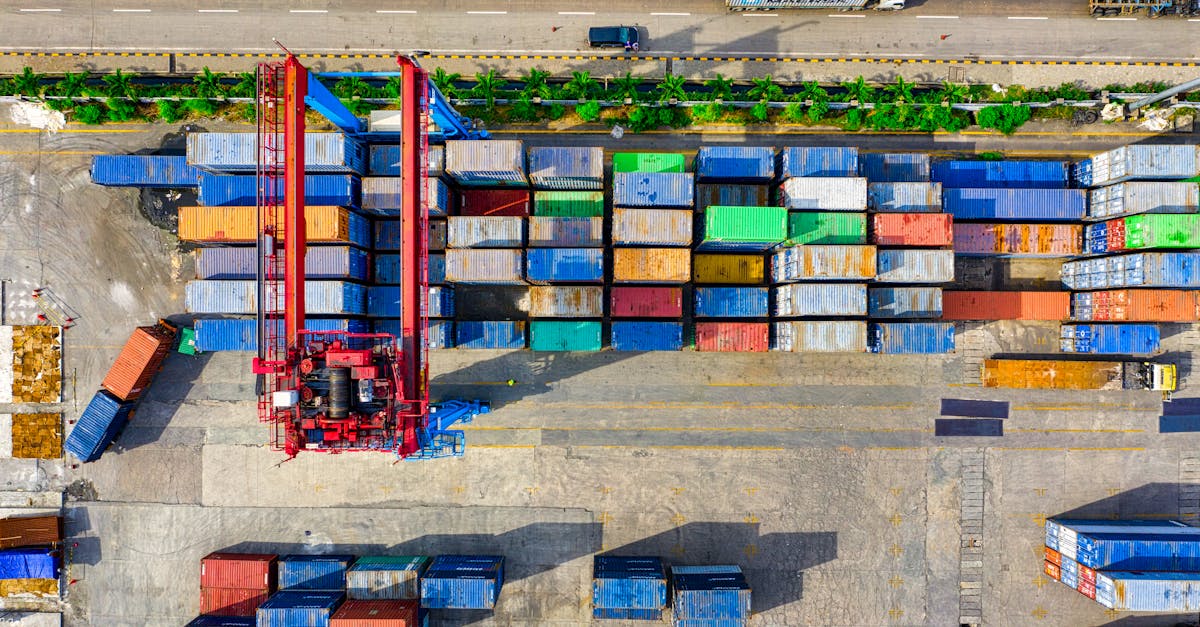
Challenges in Inventory Management
Inventory management often poses considerable challenges that can hinder a business's efficiency and profitability. One significant obstacle is maintaining an accurate record of stock levels. Discrepancies can arise from various factors such as human error, theft, or improper tracking systems. These inaccuracies lead to overstocking or stockouts, resulting in lost sales opportunities or increased holding costs for excess inventory.
Another challenge lies in demand forecasting. Businesses may struggle to predict customer demand accurately, especially during seasonal fluctuations or unexpected market shifts. This unpredictability can result in either surplus stock, tying up valuable resources, or insufficient inventory to meet customer needs, thereby damaging the company’s reputation. Addressing these challenges requires robust systems and strategic planning to ensure optimal inventory levels and enhance operational efficiency.
Common Obstacles and Their Solutions
One prevalent obstacle in inventory management is inaccurate forecasting, which can lead to either overstocking or stockouts. This issue often arises from relying on outdated data or failing to consider market trends. To address this challenge, businesses should adopt advanced forecasting tools that leverage historical data and analytics. Incorporating insights from various departments, such as sales and marketing, can also help create more reliable predictions, ensuring that inventory levels align closely with actual demand.
Another common hurdle is the lack of visibility across the supply chain. When organisations do not have real-time access to inventory levels, tracking shipments, or monitoring product turnover, inefficiencies can arise. Implementing inventory management software that provides real-time data and analytics can significantly enhance visibility. Training staff on these systems fosters a culture of accountability, enabling quicker responses to changing inventory conditions and ultimately leading to improved operational efficiency.
Best Practices for Effective Inventory Management
Effective stock tracking is crucial for maintaining optimal levels, preventing both overstock and stockouts. Companies should implement robust inventory management software to automate processes and improve accuracy. Regularly updating inventory records ensures real-time visibility of stock levels. Analytics tools can help identify trends in product demand, allowing businesses to forecast future needs more accurately and make informed purchasing decisions.
Organising inventory efficiently contributes to a streamlined workflow. Employing a systematic layout in storage areas can facilitate quicker access to items. Regular stock audits are essential to confirm that physical inventory matches recorded data. Training staff on good inventory practices fosters a culture of responsibility and attentiveness, reducing errors in stock management. Implementing these best practices can lead to enhanced operational efficiency.
Strategies to Optimise Inventory Levels
Effective inventory optimisation begins with implementing an accurate forecasting system. By analysing historical sales data, businesses can predict future demand more reliably. This approach not only helps in maintaining adequate stock levels but also minimises the risk of overstocking or stockouts. Incorporating advanced analytics and machine learning techniques can further enhance precision in forecasts. Continuous review of these predictions allows companies to adjust their inventory strategies based on real-time market trends.
Another important strategy is the adoption of a just-in-time (JIT) inventory system. This method focuses on receiving goods only as they are needed in the production process, thereby reducing excess stock. Collaborating closely with suppliers enhances the implementation of JIT, ensuring they can deliver materials promptly. Additionally, monitoring inventory turnover ratios can provide insights into the efficiency of stock levels. By identifying slow-moving items, businesses can take proactive measures, such as promotions or discounts, to clear out excess inventory and free up resources.
The Relationship Between Inventory Management and Customer Satisfaction
Effective inventory management plays a pivotal role in shaping customer satisfaction. When products are adequately stocked and readily available, customers experience fewer delays and are more likely to find what they need. This responsiveness fosters trust and encourages repeat business. In contrast, stock-outs or excessive delays can lead to frustration, driving customers to seek alternatives.
Moreover, maintaining accurate inventory levels allows businesses to anticipate demand fluctuations. Understanding customer purchasing patterns enables better decision-making regarding restocking and promotions. This alignment between supply and demand not only enhances the shopping experience but also optimises sales potential. Through precise inventory control, companies can improve their overall service quality, ultimately leading to greater customer loyalty.
How Inventory Control Affects Customer Experience
Effective inventory control directly influences the customer experience by ensuring that products are available when they are needed. Customers have high expectations regarding product availability and delivery times. When a business maintains optimal stock levels, it minimises the risk of stockouts. This reliability fosters trust and encourages repeat purchases, as customers feel confident that they will find what they are looking for.
On the other hand, poor inventory management can lead to scenarios where customers encounter out-of-stock items or extended waiting periods for backordered products. This not only frustrates customers but can also drive them to competitors. A well-implemented inventory management system helps streamline operations, allowing businesses to promptly fulfil orders and keep customers satisfied. By aligning inventory levels with customer demand, businesses can create a positive shopping experience that promotes loyalty and enhances overall brand reputation.
FAQS
What is inventory management?
Inventory management is the process of overseeing and controlling a company’s inventory, including the ordering, storing, and using of products and materials. It involves tracking stock levels, managing orders, and ensuring that inventory is optimally maintained to meet customer demand.
Why is inventory management important?
Inventory management is crucial because it helps businesses maintain the right amount of stock, reduce costs, improve cash flow, enhance customer satisfaction, and prevent stockouts or excess inventory, which can negatively impact profitability.
What are some common challenges in inventory management?
Common challenges include inaccurate inventory tracking, demand forecasting issues, overstocking or stockouts, and ineffective supply chain communication. These obstacles can lead to increased costs and dissatisfied customers.
How can businesses optimise their inventory levels?
Businesses can optimise inventory levels by implementing automated inventory management systems, conducting regular audits, analysing sales data for better demand forecasting, and establishing clear communication with suppliers to ensure timely restocking.
How does inventory management affect customer satisfaction?
Effective inventory management directly impacts customer satisfaction by ensuring that products are available when customers need them. Proper inventory control can lead to faster fulfilment times, reduced backorders, and improved overall customer experience.
Related Links
What to consider when designing a distribution centreHow to optimise inventory management in warehouses
Roundup of innovative trends in warehouse operations
Review of top automated warehousing systems on the market
7 best practices for efficient order fulfilment